
UV Sensors and Struggle Against COVID-19
By: Dr. Yakov Roizin | March 15, 2022 | Category: Technology
Disinfection using UV light is known for more than a century. In 1903, Niels Ryberg Feinsen was awarded a Nobel Prize for using ultraviolet “chemical light” against causing diseases infectious agents. Sterilization by UV radiation has been used extensively in past decades. UV radiation is very efficient in eliminating dangerous microbes in air, water and different surfaces. Covid-19 pandemic sparked additional interest in using UV light for disinfection. It was reconfirmed by several groups that ultraviolet efficiently killed viruses and, in particular, SARS-CoV-2. UVB (320-280 nm wavelength) and UVC (200-280nm) are destructive for Covid-19 RNA, while UVC with wavelength shorter than 260nm also damages the protein coats of Covid-19 viruses. The reported doses of UV radiation necessary for 99.9%-99.99% disinfection are in the range from a few to hundreds of mJ/cm2, depending on the wavelength of UVB/UVC, properties of surfaces and the specific environment. Sterilization of Covid viruses strongly stimulated demand for germicidal mercury lamps, UVC LEDs and various UV irradiating systems.
Much of the recent innovation in the sterilization field has been focused on devices for measuring parameters of UVC/UVB radiation and other types of sensors integrated in irradiation equipment. It is necessary to guarantee that the processed surfaces receive sufficient doses for sterilization. Personal items, like coats, protection masks, smartphones, banknotes etc. can be placed into enclosed sanitizers which typically are of no danger to people. The same is when ultraviolet sources are being installed in air-conditioning and water irradiating systems. This is not the case when disinfection is performed in open spaces where people are present. Therefore, UV sensors must also monitor the UV dose for the safety of people in rooms, cars, airplane cabins, etc., where irradiation is performed. Versatile types of sensors are needed for UVC/UVB sanitizing systems. Safety is difficult to achieve when handheld UVC sources are used. Portable UVC sanitizers became popular for disinfecting airplane cabins and cars and are already used by several airline and car rental companies. The challenge is how can we control and ensure that the disinfection was indeed successful? To guarantee the efficiency of sanitizing, it is necessary to measure the dose of ultraviolet in specific locations. Smart UV monitoring suggests using large number of such sensors. It is often desirable to use them as elements of wireless sensor networks.
An exemplary setting is shown in Fig.1. UV sensors integrated with RFID tags are used to control efficiency of COVID sterilization in an airplane cabin. Individual sensors installed in the positions, where high concentrations of the viruses are expected, measure the dose of UVC irradiation. An RFID reader gathers the information transmitted from RFID-enabled sensors and verifies that the sanitizing procedure is completed. Suitable sensors must have sensitivity to UVC/UVB and high UV to visible rejection ratios (low sensitivity to the visible light in the sanitized environment). As in most RFID systems, power consumption and sensor cost are also critical constraints.
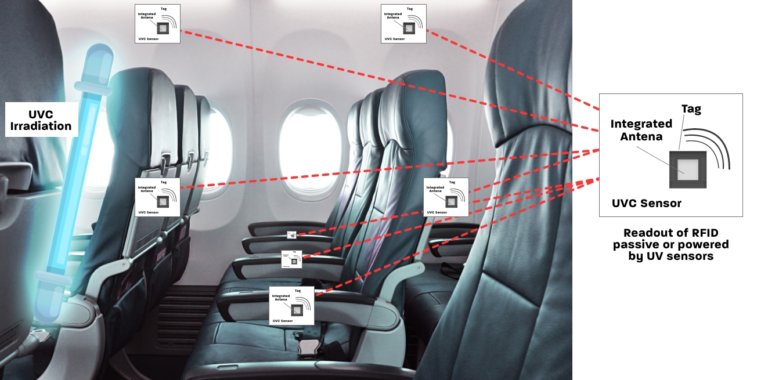
UVC/UVB sensors are needed in many other applications as well. One of the emerging applications is diagnostics of “ozone holes”, where increased amounts of ground-level ultraviolet radiation are registered due to ozone depletion effects in the atmosphere.
Solar blind photodetectors sensitive in the UV region of spectrum can be fabricated using compound semiconductor materials, such as gallium nitride and silicon carbide. These materials have a wide band gap (3.4 eV and above) and thus are not sensitive to visible light. Some of the disinfection applications can benefit from UV sensors on compound materials, especially if one or a few sensors are needed (for example sensors used to monitor the power of UVC source in order to control its degradation). However, corresponding devices are rather expensive, and complicated integration with silicon electronics for signal processing and communication is required.
It is obvious that UV sensors based on silicon are preferable for most of the mentioned applications, especially in sterilization systems requiring multiple sensors. There are several types of bulk silicon UV sensors in the market. UV sensing is often achieved by combining silicon devices responding to both UV and visible light, and reference sensors with only visible sensitivity. Reference sensors capture the background visible light and corresponding signals after normalization are subtracted from the total signal. In these cases, implementations include a system with a reference sensor on a separate chip and require integrated solutions. The main drawback of such approaches is the difficulty to suppress the visible light component and thus lack of UV selectiveness.
A promising approach is using a silicon detection layer with a thickness of hundreds of Angstroms. Such devices were built on SOI (Silicon on Isolator) wafers. Very thin Si layers are almost transparent to visible and IR light, while the UV component of light is efficiently absorbed in these Si layers. Sensing is performed by lateral PIN diodes formed in the device layer of SOI.
Tower Semiconductor has developed several novel UV sensors having high responsivity in UVC as well as featuring high suppression of UVB/UVA, visible and IR light. The corresponding solutions include devices in thin silicon layers on SOI and floating gate (FG) UV sensors. With these solutions, the voltage generated by sensors, comprising connected PIN lateral diodes in series, can reach tens of volts under irradiation, while maintaining the small device footprint. When combined with the standard CMOS UVC transparent inter-metal and passivation dielectrics, a high sensitivity to UVC is achieved.
A response exceeding 0.1A/W at 255-280 nm was demonstrated, which is more than ten times higher than that achieved in sensors currently available in the market. These sensors are manufactured as SoC with the applicable electronics integrated on the same chip.
Another type of sensors developed by Tower and successfully integrated into the standard CMOS process flows (bulk silicon, not SOI), and not requiring additional masks in production, is based on the floating gate principle.
Fig. 2 demonstrates UVC (255nm) sensitivity of a solar-blind Grilled C-sensor, one of the flavors of C-Flash NVM developed in the company.
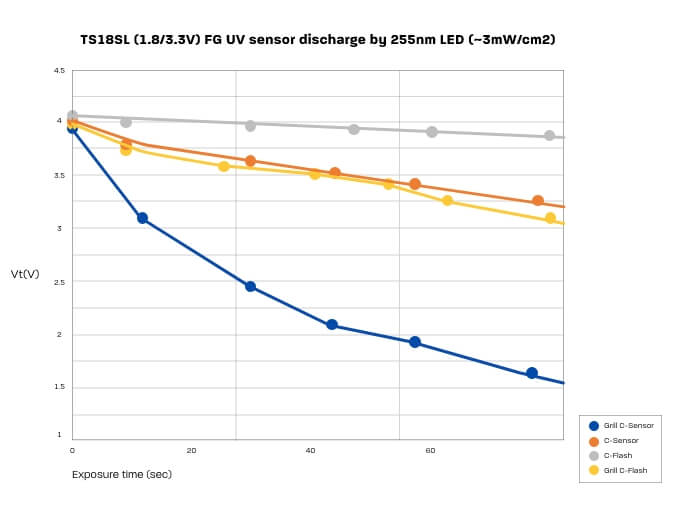
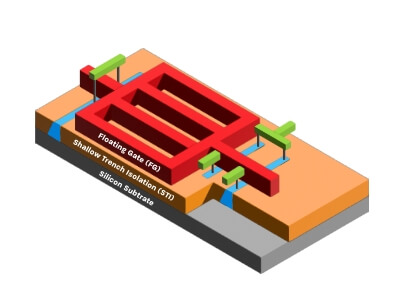
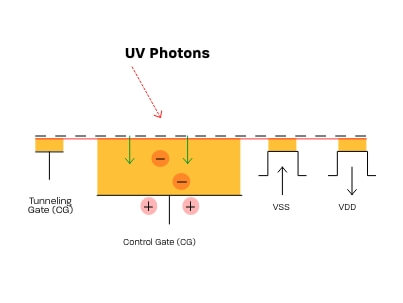
The floating gate, formed as stripes of Polysilicon on STI, is charged by tunnel injection and discharged by UVC photons. Compared with standard FG NVM, the discharge rate is strongly enhanced due to low capacitance and long periphery of the floating gates. Sensitivity practical for UVC disinfection applications is thus achieved. The device can be charged and discharged repeatedly up to 10k times.
According to marketstandmarkets, the UV disinfection equipment market size is projected to reach $9.2 billion by 2026 from an estimated $4.8 billion in 2021. The novel sterilization technologies require large numbers of UV sensors and must be quickly and affordably qualified. The focus is currently on UVC irradiation systems. As 205nm-220nm range is considered less dangerous for the human eye and is expected to have even higher disinfection effectiveness, researchers are exploring wavelengths that are even shorter than 255nm.
Silicon UV sensors developed in Tower Semiconductor are one of the critical elements in UV disinfection systems intended for struggle against Covid-19 and other emerging applications.
Dr. Yakov Roizin
Director of Emerging Technologies & Fellow
Dr. Roizin was named Tower Semiconductor Fellow, the Company’s highest technical honor, and appointed as Director of Emerging Technologies in 2010. Currently, he is working on Tower Semiconductor roadmap R&D projects and coordinating interaction with Tower Semiconductor research partners in the semiconductor industry and in academia. Dr. Roizin has served with Tower Semiconductor in various positions since 1997. Prior to his current position, he held engineering and managerial positions in Tower Semiconductor R&D departments. During his career, he supervised the development of different types of semiconductor devices, including non-volatile memories and sensors for embedded CMOS technologies.
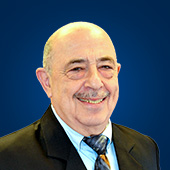