Corporate Sustainability Report 2023
To view / download the report, click here.
About this Report
We are pleased to present Tower Semiconductor’s Corporate Sustainability (Environmental, Social, and Governance) Report for the fiscal year 2023. This report highlights our commitment to sustainability, ethical practices, and social responsibility, reflecting our dedication to creating long- term value for our stakeholders.
Reporting scope and measures
The purpose of this report is to provide transparent and comprehensive information on our ESG initiatives, achievements, and future goals. It outlines our strategies and actions to manage and improve our environmental impact, social contributions, and governance practices. The ESG data performance presented in this report refers to Tower Semiconductor’s facilities only including our HQ in Migdal Haemek, Israel and our sites in the US in California and Texas. It does not cover metrics from TPSCo and Agrate facilities, which are not fully owned by Tower.
Reporting Standards
Our ESG report aligns with internationally recognized standards and frameworks, including the Global Reporting Initiative (GRI) and Sustainability Accounting Standards Board (SASB). We have also incorporated feedback from our stakeholders to ensure the report addresses the most pertinent issues facing our industry and company.
The report covers our material ESG topics as defined based on management perspective, industry norms, investor indicators and stakeholder expectations.
Data and Metrics
Stakeholder Engagement
Engagement with our stakeholders is a cornerstone of our ESG approach. Throughout the year, we have actively sought input from employees, customers, investors, suppliers, and community members. This feedback has been instrumental in shaping our ESG priorities and actions.
Looking Ahead
As we move forward, Tower Semiconductor remains committed to continuous improvement in our ESG practices. We recognize the critical role we play in addressing global challenges and are dedicated to advancing our sustainability efforts to create a positive impact on society and the environment.
We invite you to explore this report and join us on our journey towards a more sustainable and equitable future.
The report was written with the assistance of Good Vision – CSR Consulting Firm, of the Fahn Kanne & Co. Grant Thornton Group. Good Vision is highly experienced in CSR services and is a member of the GRI GOLD community and the SASB consultant content program.
Feedback
Your comments and suggestions are important to us. If you have any questions or comments about this report, please contact:
Noit Levy, Senior Vice President of Investor Relations and Corporate Communications [email protected].
The data presented in this report refer to Tower Semiconductor’s facilities only, excluding TPSCo and Agrate facilities.
Table of Contents
Letter from the Chairman of the Board of Directors
Mr. Amir Elstein, Chairman of the Board or Directors
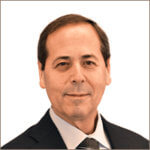
I am pleased to present Tower Semiconductor’s comprehensive 2023 ESG (Environmental, Social, Governance) report, which reflects our continued commitment to sustainability, social responsibility, and governance excellence.
The Board of Directors is dedicated to setting a strategic vision that not only addresses immediate challenges but also prepares us for the future. Our corporate strategy integrates environmental, social, and governance considerations to ensure long-term success and resilience. With considerable focus and efforts, we are on track or ahead of the previously published targets and have set a higher bar and additional new long-term targets in this report.
Our approach includes robust risk management practices, proactive climate change policies, resource conservation, and the reduction of greenhouse gas emissions. We are committed to increasing our use of renewable energy and promoting low-carbon, energy-efficient products, and materials.
We believe that high standards of corporate citizenship are essential to our mission. We foster an equitable workplace through personal development while emphasizing the importance of supporting the communities in which we operate. We invest in employee training and develop long-term programs with an ESG focus, ensuring that our corporate activities are both diverse and rewarding.
Our governance framework is designed to uphold best practices, allowing us
to continuously assess and refine our policies. The diverse skill set of our board members, coupled with their dedication to the company and belief in its growth trajectory, position us to achieve our current and future strategic goals.
I am profoundly grateful for our employees’ enduring commitment to innovation and excellence. Their dedication is the driving force behind our achievements to making a positive impact on the world and serve our stakeholders, community and industry with integrity and responsibility.
As we move forward, we remain steadfast in our mission to create value for all stakeholders through sustainable and socially responsible practices. Together, we strive to build a better, more sustainable future for everyone.
CEO Message
Mr. Russell Ellwanger, Tower Semiconductor Chief Executive Officer
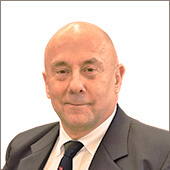
Dear Valued Stakeholders,
I am pleased to present our latest ESG report, highlighting our strong commitment to Environmental, Social, and Governance (ESG) principles. We continue to make progress to fully align our business and operational practices with our core values. Positive contributions to our environment, our society and our employees, are the backbone for the achievement of our financial goals.
Environmental Stewardship
Our dedication to environment al sustainability remains a cornerstone of our corporate strategy. We have implemented innovative practices to reduce our carbon footprint, conserve natural resources, and promote sustainable growth. Our investments in renewable energy, waste reduction programs, and eco-friendly technologies underscore our commitment to a greener future.
Social Responsibility
At the heart of our social responsibility efforts is our focus on the employee experience. Our people are our greatest asset . The impac t that the work environment has on the social, emotional, physical, and financial well-being cannot be overstated. The employee who goes home with confidence, born from having successfully met big challenges, is a much stronger contributor to their own life, family and society. We continually learn from best practices, launch multiple initiatives aimed at enhancing employee engagement and promoting diversity and inclusion, and foster a culture of continuous learning and development.
Governance and Integrity
Strong governance practices are essential to maintaining the trust of our stakeholders. We uphold the highest standards of transparency, accountability, and ethical conduct in all our operations, with Board involvement to constantly evaluate and drive implementation of best practices. Our governance framework is designed to support sustainable growth while ensuring compliance with regulatory requirements and industry standards.
The Power of Tower
This year’s corporate theme, “Power of Tower,” encapsulates our collective strength and determination to reach new heights. It reflects our superpower as an organization: our ability to innovate, collaborate and excel. As we embark on the next phase of our journey, we are confident that our commitment to ESG principles will guide us towards achieving our goals and making a lasting impact.
I would like to extend my heartfelt gratitude to our employees, partners, and stakeholders for their support and dedication. Together, we are building a more sustainable and prosperous future.
Introduction
About the Company
Vision, Mission, and Value Vectors
Our Vision
Provide the highest value analog semiconductor solutions as validated by our customers, employees, shareholders, and partners.
Our Mission
Being a trusted long-term partner with a positive and sustainable impact on the world through innovative analog technologies and manufacturing solutions.
Our Value Vectors
Partnership – We are a trusted long-term partner for customers, employees and shareholders.
Impact – We are committed to making a positive and sustainable impact on the world.
Leadership – We lead the analog ecosystem with technology and operational solutions in exciting and growing markets.
Innovation – We move great ideas into value in an environment of innovation.
Excellence embedded in everything that we do – Efficiency, Effectiveness, Quality: We pursue excellence in all we do, from ideation through product shipment. Hence, we deliver the best experience to our customers and employees.
Visit ‘History’ page, here.
Semiconductor Industry Overview
Industry Overview
Semiconductor devices have driven the rapid growth of the electronics industry over the past fifty years, becoming critical components in a wide range of applications, including computers, consumer electronics, communications, industrial, military, medical, and automotive sectors. As their performance has increased and size and cost have decreased, the use of semiconductors has expanded significantly. Suppliers now face demands for products that offer higher performance, greater functionality, smaller form factors and lower prices, all of which require increased IC complexity.
The high costs of modern fabs and the rising demand for complex ICs have led fabless companies and IDMs to seek external sources for IC production. This need gave rise to independent foundries, like Tower, that provide dedicated IC services to semiconductor suppliers. Foundries are used by nearly all major semiconductor companies as part of a strategy to diversify risk and enhance cost-effectiveness.
Foundries provide the opportunity to cost effectively supply advanced ICs to even the smallest fabless companies by creating economies of scale through pooling the demand of numerous customers. In addition, customers whose IC designs require process technologies other than standard digital CMOS, have created a market for independent foundries that focus on providing specialized process technologies. Specialty process technologies allow for greater analog content, reduced die size, and increased die yield per wafer, effectively lowering final costs. They also enhance performance, noise reduction, and power efficiency of analog and mixed-signal semiconductors compared to traditional CMOS processes
Here at Tower, we excel in this dynamic and technology-intensive environment, working closely with our customers to provide unique and specialized solutions for their business success.
Tower Semiconductor’s Offering
We provide technology and process solutions for producing ICs on silicon wafers, generally using the customer’s proprietary circuit designs. In some cases, we provide our customers with our own proprietary (IP) or third-party design elements. The end-product of our process is a silicon wafer containing multiple identical ICs. In most cases, our customers assume responsibility for dicing, assembling, packaging and testing.
We offer wafer fabrication services to fabless IC companies and IDMs, acting as a sole or second source, and enable smooth integration of the semiconductor design and production processes. This allows our customers to bring high-performance, highly integrated ICs to market rapidly and cost-effectively. We believe that our technological strengths and emphasis on customer service have allowed us to develop a unique position in large, high-growth specialized markets for CMOS image sensors, RF, power management and high- performance mixed-signal ICs.
Our production process uses specialty technologies based primarily on CMOS process platforms with added features for special and unique functionality, decreased product footprint, competitive performance and cost advantages for analog and mixed-signal semiconductors. The specialty process design infrastructure is complex and includes design kits and device models specific to the foundry and the process technology itself. Moreover, the number of foundries capable of offering specialty process technologies is limited, as few engineers have the necessary expertise, and specialty production requires significant investment for development, transfer and maintenance of these technologies. Our specialized process technologies, combined with dedicated design enablement capabilities, distinguish our services and attract industry-leading customers.
We also offer process transfer services to IDMs that wish to expand their capacity beyond using their own fabs. Our process transfer services are also used by fabless companies that have proprietary process flows and wish to produce at a secure foundry for IP protection or to diversify their production across multiple sites. Our process transfer services include development, transfer and extensive optimization as defined by customer needs.
We are a trusted, customer-oriented service provider with a solid reputation in the foundry industry for over thirty years. We have established strong relationships and partnerships with our customers. Our consistent focus on providing high-quality, value-add services, including engineering and design support, has allowed us to attract customers seeking a proven leading provider of foundry solutions. Our emphasis on working closely with customers and accelerating the time-to-market and performance of their next-generation products has enabled us to maintain a high customer retention rate while increasing the number of new customers and new products for production.
OUR STAKEHOLDER ENGAGEMENT OVERVIEW
Our approach to stakeholder engagement is multifaceted, inclusive, and designed to foster transparency, trust, and collaboration. This section of our ESG report highlights our methods of engagement, dedicated communication channels, and the steps we take to ensure approachability and inclusivity. We are committed to listening, learning, and evolving in response to our stakeholders’ needs, feedbacks and insights.
Methods of Engagement
We employ a variety of engagement methods to connect with our different stakeholders, ensuring we reach diverse groups effectively. We maintain a consistent engagement and ongoing coherent dialogue to keep stakeholders informed and involved.
Stakeholder | Engagement approach / method | |
Employees |
| |
Investors & Shareholders |
|
|
Customers |
| |
Supply Chain (suppliers/ vendors) |
| |
Communities/ Public |
| |
Academic Institutions |
| |
Business Associations |
|
Considerations for Potential Barriers
Engagement with Vulnerable or At-Risk Communities
Accessibility and Understandability of Information
Integrating Stakeholder Feedback
Customer Service
United Nations Sustainable Development Goals
Grounded in our mission to have a positive and sustainable impact on the world, we are committed to implementing the United Nations’ Sustainable Development Goals (SDG’s) to help and face global sustainability challenges. Our current activity is aligned with the following SDGs:
SDG | Tower Semiconductor’s action |
![]() | Around the world, environmental factors threaten the health and well-being of many. At Tower, we are committed to minimizing our use of hazardous substances, reducing emissions and keeping a safe and healthy work environment. Additionally, our technological capabilities relating to power management and CMOS imaging solutions are utilized in diverse medical markets and play a role in the innovation of life-enhancing medical technology. |
![]() | At Tower, our focus on providing employees with learning opportunities is at the heart of our business strategy. We strive to ensure inclusive and equitable quality education and promote lifelong learning practices. We provide our employees with ample learning programs that support their professional and personal development, including scholarships for opportunities for pursuing a relevant master degree. In addition to our internal initiatives, we also volunteer and support multiple activities to strengthen youth education at-large and with a focus on STEM. |
![]() | Tower is committed to gender equality in the workplace across the employee life cycle from recruitment, to development, to an overarching culture of inclusivity. Over the past year we are proud to have promoted women’s development through the establishment of a ‘Women’s Career Forum’ and a one-on-one mentoring program dedicated to female employees’ professional growth. As outlined in our long-term gender diversity target, we have laid out a variety of future steps to continue improving our gender equality in the workplace. |
![]() | Humanity is threatened by global water shortages and mistreatment of our marine resources. In our operations, we aim to manage and conserve water use and increase the amount of water recycled. Additionally, we closely monitor our waste water systems to make sure that they are safe and in alignment with local regulations. |
![]() | We provide our employees with a stable work environment and decent living wage and workers’ benefits. We also work diligently to protect the human rights of our workforce while providing a safe and secure work environment so that employees may focus on personal development and professional growth. |
![]() | Technological progress is key to finding lasting solutions to both economic and environmental challenges. At Tower, we provide technology solutions and manage operations that address societal demands, foster innovation and build sustainable infrastructures. Research and development are integral to our product development processes and we are proud of our partnership with leading research universities and industry consortiums that help to promote innovation across the industry. |
![]() | Achieving economic growth and sustainable development requires that we urgently reduce our ecological footprint by changing the way we produce and consume goods and resources. We are active in this effort by efficiently managing our use of chemicals and natural resources, as well as working to reduce our waste. |
![]() | Climate change is wreaking havoc and creating drastic effects on individuals, businesses and whole economies around the world. We recognize that reducing our greenhouse gas emissions is both an imperative responsibility as a good corporate citizen and a beneficial business decision that helps us reduce our transition risks. |
Governance: Responsible and Ethical Business
At Tower Semiconductor, we recognize that integrity and ethical leadership are vital to fostering a resilient and dynamic corporate culture. We are dedicated to cultivating an environment that empowers our employees to excel, our suppliers to innovate, our customers to reach their objectives, and our communities to flourish. By upholding rigorous governance standards and embracing responsible practices, we strive to ensure sustainable growth and shared prosperity for all our stakeholders.
Our Board Of Directors
As of 2023, our nine-member Board of Directors leads Tower with in-depth expertise from across diverse industries with professional backgrounds including business, accounting, engineering, and finance. Our directors’ appointments is approved by our shareholders by a majority vote of the ordinary shares present, in person or by proxy. Generally, our directors hold office until their successors are elected at the next annual general meeting of shareholders (or until any of their earlier resignation or removal in accordance with the Companies Law). In addition, our Articles of Association allow our Board of Directors to appoint others (other than external directors) to fill vacancies on our board or as an additional director(s), provided that the overall number of directors does not exceed the maximum number specified in the Articles of Association.
We are proud to share that three of our nine directors are women and all of our directors are independent except for our CEO. The Board targets recruitment of additional board members with diversity focus by 2025.
Our corporate governance documents and committee charters are publicly available on our website.
Skill/Background | Number of board members |
Semiconductor industry | 6 |
Accounting and financial reporting | 4 |
General management leadership skills | 5 |
Risk management | 5 |
Climate and sustainability | 4 |
Finance and capital market | 6 |
Academic and research | 2 |
Semiconductor operations and supply chain background | 5 |
Strategic planning | 9 |
Board of Directors Long-term Targets:
• Board Involvement with ESG: Continue our board’s involvement with ESG leadership, decision making and oversight.
• Board Member Development: Beginning in 2025, we plan to implement a learning program for the board members, that introduces them to relevant market trends and influences through lectures provided by leading industry experts.
• Board Diversity: We continue to work towards our previously stated 2025 target to have 1-2 new board members with a diversity focus.
• Board Diversity Disclosure: On-going disclosure and public transparency on the board’s capabilities and diversity through the publication of the board diversity and skills matrix on our website aligned with NASDAQ requirements.
Board of Directors
Our Board of Directors (as of end of 2023) | |||||||||
Name | Amir Elstein | Russell Ellwanger | Kalman Kaufman | Dana Gross | Ilan Flato | Yoav Chelouche | Iris Avner | Michal Vakrat Wolkin | Avi Hasson |
Age | 68 | 69 | 78 | 56 | 67 | 70 | 59 | 52 | 53 |
Role and participation in the committees | CGN | CGN and Compensation | Compensation and Audit | CGN Audit | Audit | CGN | Compensation and Audit | ||
Independent Director? | yes | no | yes | yes | yes | yes | yes | yes | yes |
Date of joining the Board | 01/2009 | 05/2005 – 04/2013 and 09/2016 to date | 01/2005 | 11/2008 | 02/2009 | 04/2016 | 06/2016 | 09/2020 | 09/2020 |
Time on board (years) | 15 | 8 years (current board residency) | 19 | 16 | 15 | 8 | 8 | 3.50 | 3.50 |
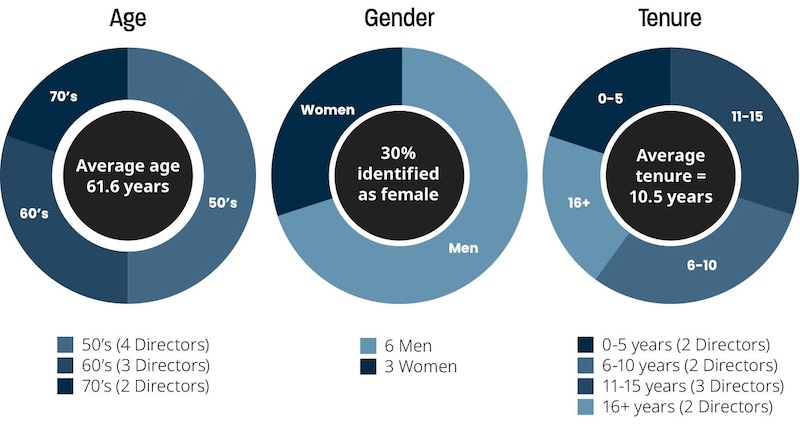
ESG Governance
Strategic management of Tower’s ESG program is overseen by the Corporate Governance & Nominating (CGN) committee of the Board of Directors. The ESG initiatives are presented to the Board of Directors and internally communicated periodically to ensure understanding of ESG impact and opportunities. The Board also review and approves our ESG reports.
ESG day-to-day management is overseen by executive leadership within the company who work with the internal team to ensure initiation of ESG focused activities, increased ESG and social responsibility awareness, as well as ongoing improvement of our practices.
Board Committees
Board of Directors Committees (as of 31/12/2023) | Audit Committee | Compensation Committee | Corporate Governance and Nominating Committee (CGN) |
Chairperson – Name | Yoav Z. Chelouche | Dana Gross | Kalman Kaufman |
Amount of committee members (#) | 4 | 3 | 4 |
Number of independent directors (#) | 4 | 3 | 4 |
Number of meetings the committee (#) | 5 | 7 | 2 |
Meeting attendance percentage (%) | 100% | 100% | 100% |
The Audit Committee oversees the transparency and integrity of the financial statements and system of internal controls over external financial reporting. This Committee assists the board in its responsibility to oversee the company’s process for monitoring compliance with laws and regulations and the code of conduct. In addition, the Audit Committee oversees the Company’s risk assessment and risk management, including procedures and activities in information and cyber security.
In 2023, the Audit Committee held a total of 5 meetings with an attendance rate of 100%.
The Compensation Committee is responsible for advising the Board of Directors with respect to the compensation of senior company employees including the CEO and all other executive officers of the company, as well as members of the Board of Directors.
In 2023, the Compensation Committee held a total of 7 meetings with a 100% director attendance rate.
The Corporate Governance & Nominating Committee (CGN) is responsible for ensuring that director appointment processes are formal, rigorous and transparent. The Committee determines criteria for the selection of Board members which ensure the Board has the proper expertise and qualifications. Additionally, the Committee assists the board in establishing and reviewing the Company’s statement of corporate governance principles and promoting good corporate governance in the Company. The Committee also works to ensure a clear and actionable succession plan for key positions within the Company and oversees the Company’s commitment to social and environmental responsibility matters.
In 2023, the CGN Committee held 2 meeting which had a 100% attendance rate.
Ethical Business Practices
Tower is dedicated to conducting its business with the highest standards of business conduct and ethics. We have an obligation to all of our stakeholders including employees, shareholders, customers, suppliers, partners, community representatives, and other business contacts, to be honest and fair in all business activities. Our Code of Conduct outlines our expectations for ethical behavior of our employees and directors. It is reviewed annually and available on our website. Additionally, we refer to the RBA supplier code of conduct for our supplier global ethical requirements.
We have designated a compliance officer who oversees that all employees are made aware of this policy and the Complaints Management Procedure by conducting a yearly ethics training. Additionally, all new employees, including part-time employees, undergo ethics training within their first 30 days of employment as part of the new-hire orientation process. Over the course of 2021 to 2023, 100% employees were acquainted with the Company’s Code of Ethics and underwent the ethics annual training.
Anti-Corruption and Bribery
Tower strictly prohibits bribery and corruption as is outlined in Tower’s Code of Ethics. Bribery can be direct or indirect through a third party, both of which are prohibited. Employees receive training on the ethics and anti-corruption policies and are requested to consult with a manager or compliance officer in any case of ambiguity regarding gifts, hospitality or donations. Tower ensures oversight of its finances through comprehensive auditing practices. Tower has a policy for non-political donations to support the local community.
During 2021 through 2023 there were no significant cases of non-compliance, in which substantial monetary fines or non-monetary sanctions were incurred.
Whistleblower Policy
Tower has a comprehensive whistleblower policy which applies to all company stakeholders, customers, employees, and vendors. The purpose of the whistleblower policy is to encourage employees and any other relevant parties to report misconduct. The policy allows prompt reporting and resolution of issues and helps foster a culture of accountability and transparency. An email is distributed company- wide annually to remind employees and on-site vendors of the policy and mechanisms in place to anonymously report concerns through a hotline available 24/7 on the Company’s website or to the employee’s manager or the compliance officer. All reports are reviewed promptly by the CLO and/or HR business partner. Tower has an anti-retaliation policy aimed at protecting employees who submit reports. All complaints and reports remain confidential, subject to any legal requirement or process.
Anti-Competitive Behavior
At Tower, we seek to compete primarily on the basis of advanced specialty analog/ mixed-signal technology, research and development, breadth of process offering, production quality, technical support, and our design, engineering and operational services. We have a highly differentiated specialty offering and proven track record in analog/mixed-signal markets, which enables us to effectively compete with larger foundry service providers. With that, our ability to compete depends on our ability to operate without infringing upon the proprietary rights of others.
During the reported period, there were no legal proceedings initiated against Tower associated with anti-competitive behavior.
Anti-Discrimination and Harassment
Tower is an equal opportunity employer and does not tolerate discrimination or harassment in the workplace. We aim to make all employees feel welcome regardless of their background and do not discriminate based on gender, ethnicity, religion, sexual orientation disability status or other differentiating factors. We promote a positive work culture and do not permit workplace bullying or harassment. In accordance with our corporate procedures, we are committed to handling and managing all cases regarding discrimination or harassment very seriously and ensure appropriate measures and disciplinary actions to be taken if needed. In 2021-2023, there were no validated incidents of discrimination. One alleged case was reviewed by the EEOC and dismissed.
Employment Collective Bargaining Rights
At NPB fab, 55% of employees are unionized. The labor agreement for Tower NPB’s union specifies several commitments undertaken by the Company.
Globally in 2023 10.7% of our employees were under collective bargaining agreements.
Prohibition of Political Contributions
Tower does not contribute to political parties across all of its global operations. Tower employees, however, are able to contribute personal funds in their own discretion. Tower does not reimburse employees for personal political contributions.
Managing ESG Risks and Improvement Opportunities
To integrate and manage potential sustainability risks and opportunities, we have implemented different procedures for risk assessment and mitigation:
1. Business Impact Analysis (BIA).
2. Risk assessment per department (including Environmental Health & Safety (H&S), compliance, HR, etc).
3. Failure Mode and Effects Analysis (FMEA) for design / technology / tools.
The procedure for global risk assessment on an annual basis uses a structured framework to identify relevant potential risks to Tower’s business, considering financial, operational and ESG related impact.
Our global QA department is in charge of reviewing, identifying, and analyzing potential risks while also implementing and managing an appropriate improvement plan to minimize potential impact to our business.
Business Impact Analysis
As part of our business impact analysis, we considered a wide range of potential threats covering several different sources, departments and risks to the business. Representatives from each department at each respective location, evaluate the severity and likelihood of occurrence of each potential risk, and those risks with the highest scores are evaluated by the department heads of the Company. They then establish risk mitigation plans for each of the high- risk areas identified.
Our global risk assessment procedures map potential risks through a rigorous process, including an identification and evaluation process.
Integrated Business Continuity Plan (BCP)
Tower Semiconductor is committed to preparedness that will allow rapid response to, and management of, potential disasters and emergencies including those that may be associated with or caused by climate change, natural disasters, technological incidents, pandemics, geopolitical instability, and supply chain disruptions. The business continuity plan ensures that programs are in place to keep critical processes running during and after unexpected events or disasters in all of Tower’s facilities. The risks associated with such events or disasters are assessed to ensure readiness: minimizing the duration and severity of such events, preventing injury, protecting assets, and enabling our ability to provide customers with a dependable and uninterrupted supply of products and services.
The plan is designed to mitigate disruption of operations, interruption of customer service and financial exposure, while promoting rapid recovery and continuation of business and activities.
The BCP consists of proactive and reactive plans to meet varying levels of business interruptions and disasters; the proactive plans include employee safety plans and day-to-day data protection activities, while the reactive plans include crisis management activities and business recovery and resumption strategies.
Tower conducts annual tests of the business continuity plan and after the results are evaluated, the BCP is updated if deemed necessary. We also track the Company’s performance during actual crises to measure effectiveness of the BCP. The plan is annually reviewed to ensure that system changes are relevant and documented.
Crisis Management Team
The CMT’s primary goals are employee safety, crisis resolution, and resumption of normal business processes as soon as possible after business interruption taking into account outside influences.
Long-term Business Risk Management Target:
While our risk assessment already covers aspects which may be affected by climate change, we plan to expand our risk assessment procedure to include a dedicated climate risk assessment component into our general BCP plan.
Protecting Cyber Security and Data Privacy
Tower recognizes the critical importance of protecting our Company and our stakeholder’s information through stringent cyber security and data privacy measures.
• Zero Data Breaches – zero known data breach
events, leaks or theft between 2021 and 2023.
• Zero Customer complaints regarding privacy – zero customer complaints regarding privacy or data loss between 2021 and 2023.
• Regular Basis Employees training on cyber and
privacy issues:
• Aligned with ISO/IEC 27001 Standard and NIST (National Institute of Standards and Technology) Cybersecurity Framework.
• Compliant with global applicable privacy regulations including GDPR.
Cyber Security
To maintain a high level of information security, we have established an Information Security Management System including control and auditing engagement, assigned formal responsibilities, and clear Company policies. The Company’s management and Board of Directors play an important role in maintaining a high level of information security and the Audit committee conducts a quarterly cyber security review including any events, remediation of any cyber security concerns and program updates. Additionally, Tower established an Information Security Steering Committee, which plays an integral role in the approval and implementation of the Information Security Policy. The Committee consists of the senior executives across different relevant departments and is presented relevant information by the CISO for decision making and planning. The CISO is responsible for providing information for periodic security review, leading the Information Security Steering Committee, implementing the Information Security policy and procedures, initiating an annual work plan, investigating and handling information security events and breaches, and presenting information security topics to management.
Tower’s Information Security Policy addresses the major risks, both technological and human, that may affect the confidentiality, integrity and availability of the information in the case of unauthorized access or a security breach. The policy outlines key elements in our Information Security Management System including information security components designed to prevent malicious or accidental damage to Company information, detection of breaches not identified by the prevention layer, real-time and post-event reaction to the breach, and documentation to analyze any events.
We provide an annual training on information security and cyber awareness for our personnel with >98% participation rate among all employees. In addition, each calendar quarter, we provide face-to-face training for all new employees on cybersecurity, among other topics. New employees are also requested to sign a form detailing permitted use of our computer resources.
Between 2021 and 2023, we had no known complaints received concerning breaches of customer privacy or identified breaches or loss of customers’ data.
Data Privacy
Tower is committed to protect the privacy and the personal information of its employees, customers, and suppliers. Tower is compliant with local privacy regulations of our business operations, including the high standards of the EU’s General Data Protection Regulation (GDPR) which protects fundamental rights of individuals related to their personal information. Tower’s privacy manager oversees the privacy compliance program and is responsible for performing periodic risk assessment and audits.
In order to offer the best service/product, we may collect, use and store certain personal data such as identification data, contact information, or technical data. This data may be collected through various methods, such as direct interaction, including forms filled out on our website and other channels such as data subject consent. We use automated technologies such as cookies and other similar technologies. Collected information is used to help diagnose problems with our server, administer our website, and deliver content tailored to our customers’ interests. Some of this is voluntary and can be disabled in browser settings.
We make sure we consider and balance any potential impact on individuals (both positive and negative) and their rights before we use or process personal information for our legitimate interests. We may share such information, subject to confidentiality obligations, with vendors, sub-processors or subcontractors working on our behalf for purposes described above, all in accordance with applicable privacy rules and regulations.
We maintain appropriate security measures in place to prevent personal data from accidental loss, misuse, alteration or unauthorized disclosure. Additionally, access to personal data is limited to those employees, contractors and third parties who are authorized to process the data on our behalf, under specific instruction, and subject to a duty of confidentiality. To ensure a company culture of privacy protection, all Tower employees are trained with respect to Tower’s privacy policy within their first 30 days of employment. All employees complete mandatory training on the privacy policy every year and renew their consent to the Company to use their personal information.
Our full Privacy Policy can be found online on our website: https://towersemi.com/about/privacy-policy/
Responsible AI Use
AI tools have seen rapidly increasing utilization across a range of personal and professional sectors. AI can enhance process and increase efficiency, however, it can also pose substantial risks which need to be managed appropriately. As of October 2023, Tower implemented a policy outlining the guidelines to using AI-based services for work activities. The policy describes the risks associated with AI use, particularly access to sensitive data, as well as inaccurate information generation. The policy also outlines correct use of AI-service in Tower to protect the business at large as well as private data of Tower’s employees and customers. All employees were informed of the basic guidelines for responsible use of AI at work.
All employees received the AI policy guidelines and were invited to a training session by an external consultant on responsible AI use and permitted functions to improve efficiency and quality of work product.
Labor and Human Rights
Tower is committed to ensuring the human rights of our worldwide employee base and treating them with dignity and respect as defined by the international community. Tower prohibits forced labor and human trafficking. Our suppliers are obligated to conduct their business in an ethical manner and to act with integrity and in accordance with the Responsible Business Alliance Code of Conduct to which Tower is committed and complies with.
Tower has identified a no-trade list of global countries which are at a high risk of ethics violations including human rights. Tower has set preventative restrictions on sourcing from these countries to help promote a responsible and reliable supply chain including the conflict minerals program. We prioritize regional sourcing to support local economies, enhance supply chain transparency, whilst ensuring stringent labor and human rights standards.
Tower has in place a human rights policy under the responsibility of the compliance officer. The policy addresses the following subjects:
• Freely Chosen Employment
• Child Labor Avoidance
• Working Hours
• Wages and Benefits
• Humane Treatment
• Non-Discrimination
• Freedom of Association
• Anti-slavery
Tower’s code of ethics includes an anti-slavery policy which must be reviewed and acknowledged by all suppliers before conducting business.
Cooperation with the RBA
Tower is dedicated to maintaining a responsible supply chain and sourcing from high-quality ethical business partners. Tower has been working alongside the Responsible Business Alliance (“RBA”) since 2014 to promote transparency and customer accessibility to social responsibility data and performance. The RBA provides assessment tools designed to help members identify social, environmental, and ethical risks in their supply chains, and implement systems to further improve their social contribution. Tower participates in the RBA self-assessment questionnaire (“SAQ”) for all of its facilities every year and works to improve based on input collected. We have been recognized by certain Tower customers for our noteworthy rating and improvement since completing the first SAQ. The risk level assigned to Tower from such assessments is low.
For our supplier global ethical requirements, we use the RBA supplier code of conduct.
Conflict Minerals Policy
Tower is committed to the responsible sourcing of minerals and we support the position of the Global e-Sustainability Initiative (GeSI) and Responsible Business Alliance (RBA), that require companies to avoid the use of conflict minerals that directly or indirectly finance or benefit armed groups in the Covered Countries.
The Company has established programs aligned with the internationally recognized OECD due diligence framework to regularly evaluate our supply chain and require our suppliers to do the same. Suppliers are prohibited from supplying us materials known to be derived from the Democratic Republic of the Congo (DRC) or adjoining countries that have not been confirmed as “DRC Conflict-Free” via a recognized and credible third-party process, such as the Conflict Free Sourcing Initiative’s Conflict Free Smelter Program (CFSP).
At Tower, we use tantalum and tungsten. We require our suppliers to implement policies and due diligence measures that will assure that products and components supplied to us containing such minerals are conflict free. In addition, we require our direct suppliers to provide us with completed conflict minerals declarations (CMRT). We are committed to taking appropriate actions to enforce this policy, including discontinuing purchases from suppliers that fail to comply with this policy. Based on information provided by our suppliers, we do not knowingly use any non-conflict free minerals in our operations.
Tower is dedicated to maintaining compliance with local laws, including SEC regulations on conflict minerals, and publishes its conflict minerals report on an annual basis as required.
Supplier Audits
To evaluate our suppliers’ quality system and to verify that appropriate controls are in place, we established an audit procedure for both new and existing suppliers of raw materials. Each new supplier of raw materials undergoes an audit during the approval period; and all existing suppliers of raw materials undergo an audit every 3 years.
The audit assesses the suppliers’ processes including the following categories: Quality Systems, Supplier and Materials Management, Product Control and Traceability, and BCP (Business Continuity Plan). The audit evaluates ESG aspects, including transparency, labor systems, H&S practices and ethics.
The assessment is performed by both the supplier itself and Tower. Suppliers that receive a score below 70% are subject to probation. Tower strives to integrate sustainable practices into its supply chain and uses audits as one method to establish a dialogue with suppliers for improving their sustainability practices.
Supplier Feedback Scorecards
Tower utilizes a Global Supplier Performance Scorecard to rank the performance of its selected strategic suppliers annually. The process is led by the purchasing department in collaboration with the QA department and helps Tower provide feedback to its suppliers, communicate clear expectations for improvements, and enhance our supplier relations.
The scorecard is divided into four main sections:
• Quality – Product & Safety
• Service & Support
• Cost
• Supply Chain
Facilitating a Sustainable Future
Tower offers a broad range of advanced analog process technologies tailored to meet its customers’ precise specifications, enabling the most cost-effective and versatile IC technology and process platforms.
We are proud to have an environment of innovation which allows us to lead the analog ecosystem with technology solutions in exciting and growing markets.
The variety of end-products attained thanks to our specialty technology offerings include 5G wireless communication, Wi-Fi, Bluetooth, global positioning system (GPS), electric vehicles, medical technologies and more.
How We Support Sustainable Technology
- Wireless Everything Seamless Connectivity – 32% of 2023 Corporate Revenues
- Green Everything Energy Efficiency – 39% of 2023 Corporate Revenues
- Smart Everything Interactive Smart Systems – 20% of 2023 Corporate Revenues
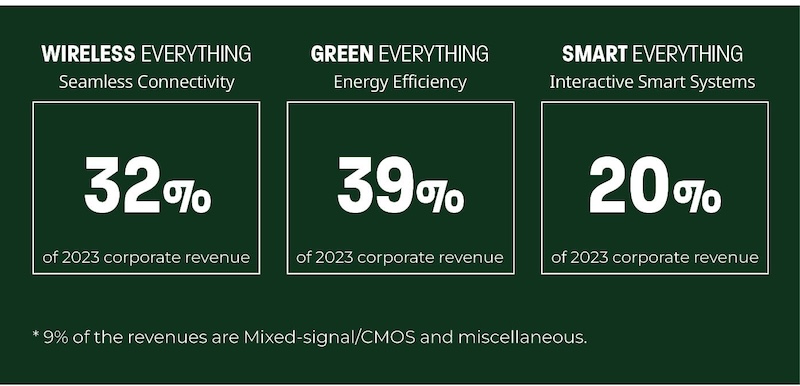
Through wireless, green and smart aspects, our technology helps facilitate and promote a sustainable future in numerous ways including:
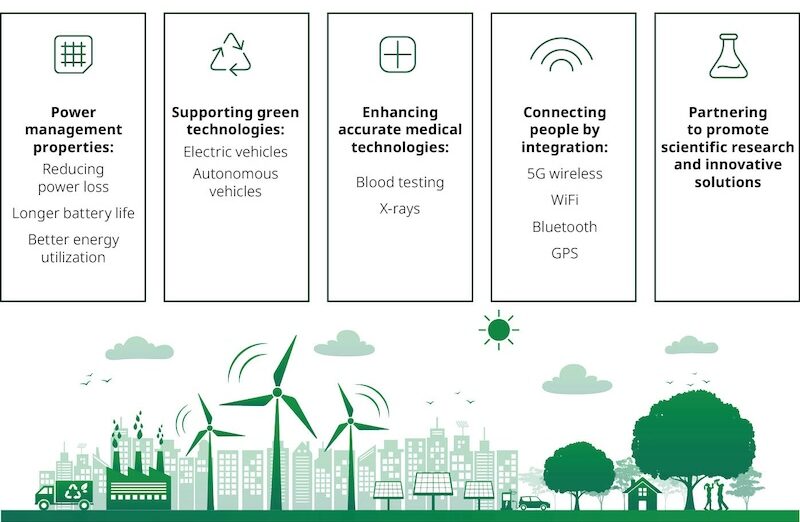
Our Process Technology Offerings
RADIO FREQUENCY AND HIGH-PERFORMANCE ANALOG: Enabling a New Era of Communication We provide industry-leading, low-loss, high-dynamic range technologies from wireless RF to mmWave communications. Our SiGe BiCMOS, RF-SOI and RF-CMOS technology solutions enable high-speed, low-noise and low-power products for consumer, infrastructure, and automotive applications. |
POWER MANAGEMENT: Empowering Efficiency – Shaping Tomorrow Our power management platform provides highly modular, industry-leading BCD technologies, with best-in-class power efficiency across a wide range of voltages; delivering comprehensive solutions for the consumer, industrial, infrastructure, automotive and medical markets. |
CMOS IMAGE SENSORS: Cutting Edge Imaging Solutions Customized for Your Needs We offer high-end, state-of-the-art technology solutions, unique customization processes and unmatched design flexibility, which enable performance- optimized pixel technology with advanced features and reduced die size, addressing automotive, machine vision, high-end photography and cinematography, medical, 3D, AR/VR and security applications. |
SENSORS AND DISPLAYS: Expand Your Sensing Capabilities Beyond Imaging – Lead the World of Sensors Our proven and flexible capabilities and technological platforms enable fabrication of diverse sensing devices consisting of unique ionizing radiation sensors, remote temperature sensors, magnetic (TMR), UV radiation and gas sensors. In addition, we supply technology for LCOS and OLED on silicon display backplanes with dedicated flows for high-brightness micro-displays. |
AUTOMOTIVE: Innovative Analog Solutions for Smarter Automobiles Our broad range of mature and modular analog technology platforms for sensors and displays, wireless and wireline communications, mixed signal and power management provide the most comprehensive and advanced solutions for electric autonomous vehicles. |
Wireless Everything
RADIO FREQUENCY (RF) & HIGH-PERFORMANCE ANALOG (HPA) TECHNOLOGIES
Enabling A New Era Of Communication
Tower Semiconductor has been an industry leader in delivering semiconductor technologies that help connect everything, everywhere and all the time. Starting with the ubiquitous high-speed wireless communications we take for granted today in much of the world (e.g. WiFi, 5G, Satellite), Tower’s radio frequency Silicon-on-Insulator technology (RF SOI) and Silicon-Germanium (SiGe) technologies have been the go-to choice for customers worldwide for many years. Tower’s high-performance SiGe and SiPho technologies are the fundamental building blocks essential to move data around through vast copper and fiber-optic wired infrastructure at astonishing speeds to give us a seamless and uninterrupted internet experience. Additionally, today’s expanding Artificial Intelligence “training and inference” clusters heavily depend on the optoelectronic components designed and manufactured in Tower technologies to give us far improved quality of service in all walks of life. And finally, RF and optical sensors designed in Tower’s technologies are integrated into everything around us to improve our everyday lives: from smarter vehicles to smarter factories to smarter healthcare. Taken together, Tower’s RF and HPA technologies are helping bring the world together through high-speed connection, improving quality of life, and minimizing environmental impact.
Tower’s RF and HPA technologies are transforming communication by connecting everything in the world more efficiently, cost-effectively, and with lower power, benefiting both society and the environment. Our platforms are integral to numerous communication technologies that offer significant environmental and social advantages.
Technology offering: • RF SOI platform | Environmental / Social Benefits WiFi / Bluetooth technologies reduce superfluous wires that find their way into trash hurting wild and marine-life. |
GPS technology increases productivity and reduces carbon footprint in multiple sectors. | |
The sensors used in Radar and LiDAR Vehicle-to-Everything (V2X) communications, that Tower Semiconductor helps bring to market, are critical in reducing millions of global fatalities caused by distracted drivers and drunk driving. | |
Higher performance and lower power RF front-end technologies reduce power consumed in transmitting and receiving 5G RF signals, thus enabling longer battery life. | |
The platforms used for datacenters (clouds), high-speed optical telecommunication, and 5G communication enable stable and high-speed connections that have transformed work places and allowed hybrid-work mode that has not only reduced environmental impact (e.g. traffic congestion) but also improved quality of life for working adults tending to young children or elderly. |
Green Everything
Tower’s power management technologies play a crucial role in sustainability and promoting green practices across various industries. Power ICs are central to this effort, enabling green technologies and products. In addition to optimizing energy usage, solutions for increased electrification serve as a cornerstone of sustainable power development, driving the transition to greener technologies across various sectors.
Technology offering: • Power technologies | Environmental / Social Benefits Tower’s power management technologies optimize the efficiency and reliability of a wide variety of electrical systems such as electric transportation, electric power tools, consumer battery operated devices, renewable energy systems, data center power delivery and many more. Tower offers best-in-class BCD technologies that focus on increasing power efficiency to reduce power energy losses, and ensure longer battery life and better energy utilization. In addition, power management technologies enable high- power capabilities for powerful electric motors and high- performance computing with high-power consumption. |
Tower’s power management platforms are designed for maximum flexibility, enabling customers to produce a design-optimized product at any desired level of integration and achieve first-pass success for fast time-to-market. | |
By offering each of our BCD technologies, the 180nm BCD and the 65nm BCD, in two sites worldwide, we provide maximum operational flexibility, ensuring uninterrupted product supply and geographic diversity. | |
The 65nm BCD offers best-in-class digital integration together with high-power capabilities addressing the growing demand for optimized power solutions. The 180nm BCD offers high-voltage solutions supporting 48V systems, enabling high-power capabilities and efficient battery management IC solutions for a wide variety of markets. |
Smart Everything
Semiconductor products influence almost everything in people’s daily life – the way people communicate, operate home appliances, process data, receive healthcare services and more. Tower Semiconductor continues to advance its semiconductor technologies, enabling its customers to fabricate novel products critically important for society. Tower’s innovations allow more capable and energy efficient solutions, thus increasing the quality of life and building a sustainable society.
Technology offering: • Nano-sensors | Environmental / Social Benefits These technologies can be used for controlling and/or monitoring physical activity (running, jogging, etc.) and testing of food quality. They can benefit human healthcare by leading to more effective treatment for sepsis, shorter hospital stays, reduced mortality and expedited blood testing. |
CASE STUDY
METABOLIC DATA MEASUREMENT BIO-CHIP TECHNOLOGIES
Tower develops smart biosensors featuring special low-power consuming transistors with open surfaces. One type of such sensors which Tower’s researchers have developed in cooperation with several Israeli companies and academia groups, are medical devices used for continuous monitoring of blood sugar. Improving this technology has life enhancing effects for individuals
who need to monitor their blood sugar levels empowering them to make better health decisions. The nano-sensors fabricated using Tower’s technology (special nanowire devices on SOI platform) enable continuous access to critical metabolic data. Together with consortium partners, we published several papers in Tier 1 journals and filed patents on the express low-cost sensing of Estriol, PSA, Ferritin, etc. using ultra-small drops of blood.
Collaborating For a Better Future
Tower is dedicated to promoting a global environment of innovation and collaboration that stimulates the discovery of breakthrough solutions addressing the challenges of today and tomorrow. We are proud to take an ongoing part in numerous prestigious consortiums and collaborations with world-leading academic institutions in the US, Europe and Israel that explore in parallel both novel technical ideas and sustainability solutions.
CERN – Intergovernmental Research Organization
Our radiation sensing technologies are applied to several novel applications in the field of radiation science and space including research performed by CERN organization.
Tower Semiconductor is honored to contribute to the development of “the world’s largest and most complex scientific instruments to study the basic constituents of matter”. Our technologies’ utilization in these instruments help to study the origin of the universe, how it works and what it is made of. In particular, Tower developed sensors for the ALPIDe platform for ALICE (one of the large hadron detectors in CERN).
Nemo Consortium On Neuromorphic Chips
Tower Semiconductor participates and leads the Device Cluster of the Israeli Innovation Authority NEMO consortium. The activities of NEMO aim to build full neuromorphic computing systems integrated with sensing capabilities. This technology is expected to lower power consumption for information processing by sensors by an order of magnitude compared with the existing processes.
For this research, our team alongside the Technion Israeli Institute developed special memristors, electrical components which emulate the synapses connecting the real nerve cells. Edge sensors fabricated in Tower devices are used for smart processing of information used for this research. Tower’s papers on the technology were published in the Nature Electronics research journal.
The outcome of this novel devices is low-cost neuromorphic chips suitable for mass applications in sensing systems. These developments will be able to contribute to environmental, social and scientific goals. They offer important sustainability advantages as they allow for significant decrease in the energy required for data processing- an area which has seen steady growth in global demand over recent years.
Metamaterials Consortium
In 2024, Tower has joined the IIA metamaterials Consortium. The main goal of the Consortium is to develop novel technologies for the fabrication and implementation of Meta-Materials and Meta-Surfaces. Additionally, the consortium’s purpose is bridging the existing gap between academic studies and practical implementation of metamaterials in the industry. Tower brings to the consortium its experience in photolithographic techniques and materials available in our CMOS production facilities. The work is focused on the development of recipes supporting the requested metamaterial structures designed by our partners. This includes the modification or adjustment of deposition and etch recipes, defining of masks for lithography and modeling of optical effects. We also target demonstrating feasibility of novel applications critical for society, such as optical instruments which extend human vision, in particular extended reality (XR) devices.
Looking Ahead to the Next-Generation of 3D Medical Imaging
Together with its customers, Tower is engaged in the development of advanced sensors for 3D medical X-Ray imaging systems. This enables higher quality X-ray images at lower doses absorbed by the patient body. Currently, we applied for an EC consortium (together with several leading European companies), with the aim to build a next-generation of 3D imaging systems employing the wafer bonding technologies developed in Tower. We strongly believe that this and similar projects will additionally contribute to the well- being of the world’s community.
Talks and Publication
Tower Semiconductor engineering experts serve as members of technical/scientific committees and reviewers of leading international journals and scientific conferences, such as IEEE IMW, Electronics and IEEE ED. In addition, every year numerous scientific papers by Company engineers are published in various journals and invited talks are presented in leading technological forums, panels and conferences worldwide.
Environmental Responsibility
In an era marked by rapid technological advancement and global connectivity, the semiconductor sector stands at the forefront of innovation.
While the growing use of semiconductors promises to advance sustainable technology implementation in various sectors as described in our ‘Approaching a Sustainable Future Chapter’, their production process
does have environmental externalities. We recognize our responsibility to mitigate the environmental impact of our operations and aim to reduce our resource consumption and emissions through the implementation of sustainable management practices. We focus our environmental impact activities on reducing energy and related GHG emission, hazardous waste and water usage. Additionally, we also work to minimize product life cycle impacts through innovation in product design and careful management of our supply chain.
By integrating environmental stewardship into our business strategy, we aim not only to minimize our ecological footprint but also to reduce risks and foster a resilient business future.
Our Long-Term Environmental Impact Strategy
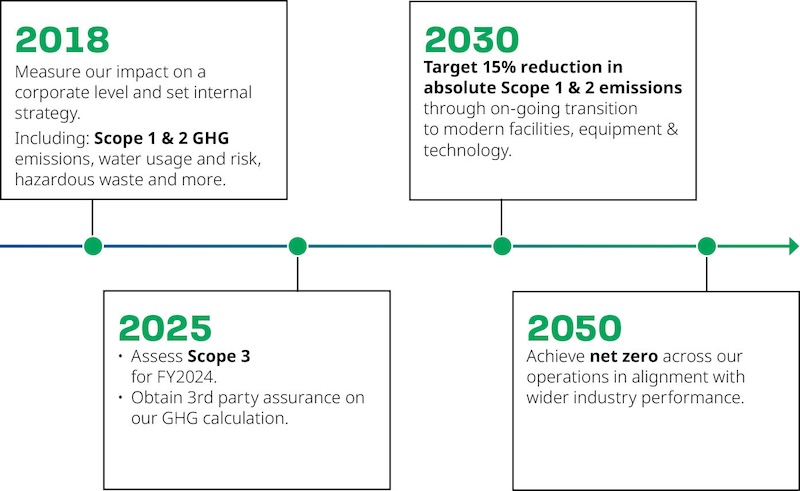
Where we are today | Our Goals (in reference to the base year 2022) | |
GHG Emissions | 412 thousand tCO2eq Scope 1 & 2 in 2023 | 15% reduction in absolute Scope 1 & 2 emissions by 2030 and net zero by 2050 |
Renewable Energy | ~20% renewable electricity from the local grid globally | 100% renewable electricity by 2050 |
Hazardous Waste | 6.8 tons generated of which 3.4 tons were recycled | Reduce hazardous waste by 20% by 2030 compared to 2022 base year |
Monitoring and Measurement | Closely measure our environmental impact across all material areas | Continue upholding our tracking and monitoring practice and expand to include Scope 3 emissions in our GHG tracking |
Data Validation | Work with a 3rd party consultant vendor on our data tracking and ESG reporting | Obtain 3rd party assurance on our GHG calculations and report to the Carbon Disclosure Project (CDP) by 2030. Submit our GHG emission reduction targets and strategy for validation by the Science Based Target Initiative (SBTi) |
Management Oversight and Compliance with Environmental Regulation
Each site has a person responsible for environmental management, reporting to the operations site manager and with a dotted line reporting to the Corporate SVP of Excellence.
Tower operates in accordance with the required local environmental laws and regulations. All required environmental permits and registrations are obtained, maintained, and kept current. In addition, all applicable operational and reporting requirements are followed, including waste treatment, use of hazardous materials, protection of hazardous materials and emergency preparedness.
During the reported period, we had no complaints, legal proceedings, or fines regarding environmental issues in Israel or the US.
Environmental Audits
Our US and Israel sites are certified according to the ISO 14001 environmental management system standard, which offers an effective and comprehensive oversight for environmental management processes.
Emission and waste water quality tests are conducted on a weekly, monthly or yearly basis, in accordance with the requirements set forth by various regulatory bodies. Additional audits are performed to manage safe and responsible disposal of hazardous materials.
Employees’ Training on Environmental Issues
All employees who are involved in production are appropriately trained on environmental matters by the H&S department. Training topics include environmental responsibilities, documentation and compliance, ISO 14001, hazardous materials’ release, air quality, facility emissions, resource consumption, waste management and storm water quality.
Circular Economy and Life Cycle Analysis
The expanding use of semiconductors in the economy has significant potential impact on the environment across different stages of their product life cycle.
This life cycle can be divided into five key phases:
- Sourcing, processing and supplying raw materials – this includes extracting and refining the raw materials needed to produce semiconductors; for example, mining silicon and processing it into pure silicon wafers.
- Production – this involves the actual processing of semiconductor devices; for example, processing on silicon wafers in our fabs.
- Putting into circulation – transporting, distributing and marketing efforts – this phase covers the logistics and marketing necessary to bring semiconductors to market. An example is shipping finished semiconductor products to manufacturers worldwide.
- Use, reuse, and product maintenance – this stage includes the deployment of semiconductors in various devices and their maintenance. For example, semiconductors are used in consumer devices, like smartphones and their periodic software updates.
- End- of-life management (recycling and disposal) – this involves the processes for managing semiconductors once they are no longer usable. An example is recycling old devices to recover valuable materials.
Tower is responsible for the first two phases of the life cycle: sourcing, processing and supplying raw materials, as well as production. The subsequent phases – transportation, distribution, marketing, use, reuse, product maintenance and end-of-life management are the responsibility of our customers, product value chain, end users etc.
As a company providing semiconductor solutions, we continuously strive to help our customers reduce the environmental impact of their products through better energy efficiency, responsible operations, sustainable product sourcing, effective water management and comprehensive waste management. Tower is committed to minimizing the carbon, waste and water footprints throughout the life cycle of its semiconductor technologies’ processes.
Environmental and Climate Risk Management
Climate change brings with it a variety of environmental risks that may negatively affect Tower’s business operations, the communities within which we work and the wider global ecosystem.
Tower strives to manage these risks and reduce potential adverse environmental impact on our operations in order to protect long-term value and operate our business as sustainably as possible.
Transitional and physical climate-change related risks, as well as other environmental risks, are monitored and mitigated through our environmental management system and business continuity plan.
Transitional Risks
Transitional risks include legislative developments mandating a reduction in greenhouse gas emissions which may result in increased energy prices and higher costs for transportation, equipment and raw materials. GHG emission caps and taxes could apply directly to the company or indirectly through stakeholder expectations. Our target to reach net zero by 2050 and interim reduction targets as outlined in our ‘Environmental Impact Strategy’ will help minimize our transitional climate risks. Tower is subject to a variety of laws and regulations relating to the use, discharge and disposal of toxic and other hazardous materials. Legislative compliance is critical to the risk-management of the Company.
Physical Risks
Climate change also poses direct physical risks due to increased patterns of extreme weather patterns such as droughts, floods, wild-fires and rising sea levels. These may impact transportation and production across many industries. While the scale of these challenges is difficult to predict, Tower recognizes the risks presented by these developments and the need to monitor and adapt to ongoing environmental changes. Our ‘Business Continuity Plan’ (BCP) reviews among other potential risk interruptions due to natural disasters, and outlines both preventative measures and assesses such risks, and reactive measures to ensure business continuity even under extreme circumstances. You can find additional information on our BCP in our governance chapter under ‘Managing ESG Risks and Improvement Opportunities’.
GHG Footprint and Energy Management
We recognize that greenhouse gas emissions released throughout our production process and supply chain contribute to climate change. We are committed to producing as responsibly as possible while maintaining business efficacy.
The Intergovernmental Panel on Climate Change (IPCC) releases regular research reports and recommendations which guide global governmental and business decisions on climate change, mitigation and adaptation. We align with the IPCC guidelines and recommendations targeting climate neutrality by 2050, and plan to have our targets validated by the ‘Science Based Targets Initiative’ (SBTi).
Tower sees great importance in reducing its carbon footprint in alignment with recommendations from the international scientific community, including the IPCC guidance to limit warming to an average of 1.5ºC as was agreed in the Paris treaty on Dec. 2015.
GHG Reduction Long-term Targets:
15% reduction in absolute Scope 1 & 2 emissions by 2030 and net zero by 2050
Our GHG Footprint
To address the rise of greenhouse gas emissions associated with energy consumption, the world must prioritize greater reliance on renewable energy and enhanced energy efficiency. With this in mind, Tower’s commitment is embedded in its ongoing business activities.
Tower has been monitoring its GHG footprint according to the ‘Greenhouse Gas Protocol’ since 2018. Currently, we measure our Scope 1 and 2 carbon footprints, with plans to begin measuring Scope 3 for FY2024.
- Scope 1: Scope 1 emissions are greenhouse gases a company puts into the atmosphere from its own property. Our total Scope 1 emissions were 344 and 257 metric tons respectively in 2022 and 2023.
- Scope 2: Carbon emissions from purchased electricity. Our total Scope 2 emissions were 131 and 155 metric tons respectively in 2022 and 2023.
- Scope 3: We will commonsense reporting the emissions from our entire value chain, including suppliers and product use by customers, as of FY2024.
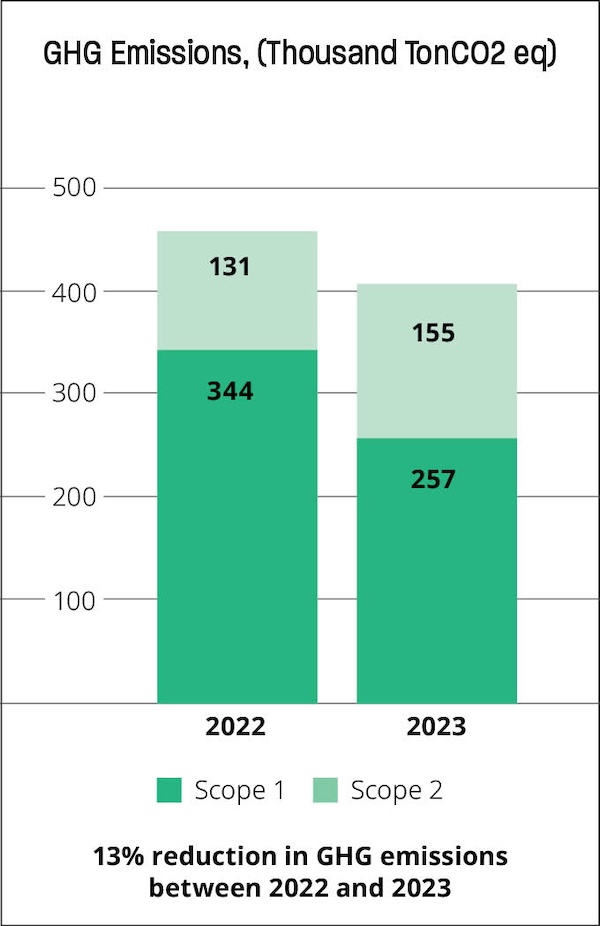
Energy Management
To address the rise of greenhouse gas emissions associated with energy consumption, the world must prioritize greater reliance on renewable energy and enhanced energy efficiency. With these concerns in mind, Tower is committed to addressing these issues in its ongoing business activities.
2022 | 2023 | |
Energy consumption (total), GJ | 1,939,744 | 2,265,952 |
Electricity consumption, GJ | 1,814,305 | 2,147,726 |
Renewable energy from the Grid , GJ* | 325,427 | 404,729 |
Fuel consumption, GJ | 125,438.75 | 118,226.36 |
Renewable Energy
We are regularly evaluating options to grow our renewable energy share across our sites based on local availability and other determining factors. In 2019, Tower installed a photovoltaic (PV) system in a nearly 100,000 square foot area in our Israeli facilities with 1700MWh potential yearly production of solar energy.
Additionally, as renewable energy continues to grow globally across many municipal grids, our portion of electricity produced from renewable energy has increased consistently over the last few years. From 2022 to 2023 the percentage of renewable energy from the grid at our operation sites grew by 24%.
We are seeking to supplement the local growth in the renewable energy grid through additional renewable energy acquisition in the coming years.
Additionally, we are also evaluating options for increasing our renewable energy beyond the grid level threshold. We are assessing how we can implement further energy efficiency practices to reduce our overarching energy consumption in future years.
Our fuel consumption consists of diesel, unleaded gasoline, LPG and natural gas (VOC, boiler, steam and chilled water). Our total fuel consumption decreased by 6% from 2022 to 2023.
Increasing Efficiency with LED Bulbs
We know that efficiency is not only environmentally sound but also good business. In 2023, we undertook a significant light fixture upgrade where we changed over 400 bulbs to LEDs at our Texas site. This will result in approximately 64 thousand kWh saved annually totaling about five thousand dollars savings annually.
*Renewable energy usage is estimated based on the local municipalities energy power mix rate for renewable energy. The percentage renewable energy rate per site is then translated to the total renewable energy of the company.
Water Management
Water is becoming an increasingly scarce resource globally due to population growth, urbanization and climate change. This scarcity poses specific challenges for the semiconductor production process, which requires substantial quantities of “ultra-pure” water for cleaning hardware and removing chemicals used during production.
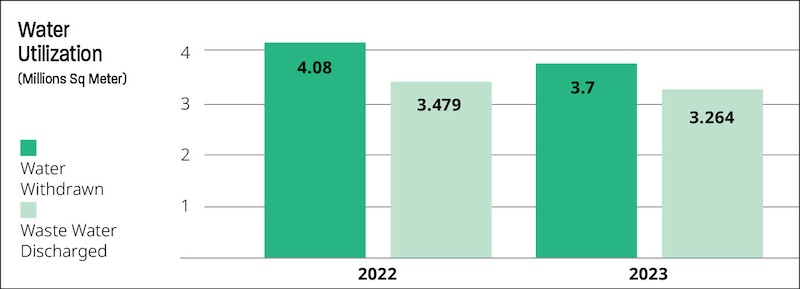
Tower is consistently working to enhance its water treatment and management practices to maximize water conservation throughout the production process.
Water Stress
Water stress, a condition that arises when the demand for water surpasses the available supply during a specific period or when poor quality limits its usability, has increasingly become a concern for Tower. Effective planning is crucial in managing the potential impacts of water scarcity, including higher supply costs and social tensions with local communities.
It is especially challenging to ensure consistent water access for operations in water-scarce regions. According to the World Resources Institute’s (WRI) Water Risk Atlas tool, Aqueduct, our facilities in Israel and Newport Beach face extremely high water stress, while the stress level is medium-high in Texas.
Given the varying impacts of water use by location, Tower has implemented strategies to reduce water consumption and enhance water recycling at each of our sites worldwide.
Water Recycling
Since semiconductor production processes are water intensive, we are always looking for ways to recycle our water so we can reuse it internally within our own operations and reduce the amount of water withdrawn. From 2021 to 2023 we recycled some 856 thousand cubic meters of water annually through some of the following water recycling initiatives:
• One of our primary water recycling method at our Newport Beach, California site is recycling reverse osmosis (RO) reject water (the concentrated non- pure stream of water remaining from the reverse osmosis water purifying process).
• In Newport Beach, California we also reuse rinse water that is taken from wet sinks, in abatement tools and scrubbers
• At our Israeli sites in Migdal Haemek, we recycle 60% of the ultra-pure water.
• In San Antonio, Texas, we collect the water from humid air extracted during the process of creating the dry indoor environment needed for chip production. This saves tens of thousands of m3 of water per year.
856 thousand m3 of water recycled annually between 2021 and 2023
Waste Management
Tower is committed to reducing waste generated throughout the semiconductor production process, including hazardous and non-hazardous waste. The most material waste stream from our production is waste water (discussed above) and chemical solvents. In addition, we also have a smaller amount of waste from our office operations. We regularly evaluate our process for potential waste reduction and recycling options and partner with authorized high-quality waste management companies to ensure that waste is disposed of responsibly and in accordance with local regulation.
At our Newport Beach, California site, we have established a ‘Waste Minimization Committee’ which is composed of our Environmental Compliance Lead, facilities and operations managers, and relevant engineers. The committee is responsible for developing and implementing our ‘ Waste Minimization Plan’ which is also submitted every four years to the state authorities according to local regulation. The waste plan covers a waste stream assessment, minimization targets, reduction methods and the evaluation of progress over time.
Non-Hazardous Waste | 2022 | 2023 |
Total Waste Generated (Tons) | 426 | 365 |
Waste Recycled (Tons) | 47.91 | 45.89 |
Hazardous Waste
Our business is subject to a variety of laws and governmental regulations relating to the use, discharge and disposal of toxic and otherwise hazardous materials used in Tower’s production processes.
We have in place strict measures that ensure and promote safe use and disposal of all hazardous materials. This procedure includes a profiling process for each material used and the registration of waste items with local regulatory authorities as required. We work to minimize water content in solvent waste generated during our production process in order to reduce the total amount of solvent waste disposed. Additionally, we work to ensure safe material disposal even beyond local regulations to ensure safe material disposal. For example, at our San Antonio, Texas site, we chose not to use any deep well injection of solvent waste which may pose risks to local communities in the future and instead we pay for the responsible waste-to-energy disposal of our solvents. Our partners at ‘Clean Earth’ provide us with certificates of waste disposal which allows us to monitor materials used through end-of-life.
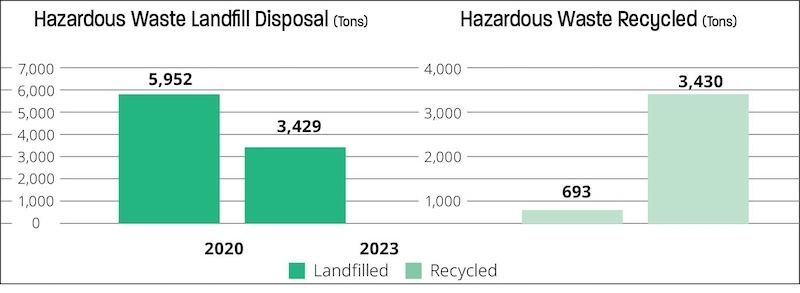
42% reduction in hazardous waste landfilled through increasing innovative recycling methods.
50% diversion rate of hazardous waste in 2023.
To enable a secondary use of sulfuric acid waste material used in our production, we have developed and constructed a system for the removal of hydrogen peroxide from used sulfuric acid. Sulfuric acid, which was previously disposed of as hazardous waste, is turned into a diluted technical acid and can be sold as a new raw material. This reuse process has been in place in Israel since 2020.
Another project implemented in 2020 is treatment by reverse osmosis of brine after regeneration of ion exchange resin. This treatment helped us cut brine disposal by half and avoid disposal of approximately 2,000 m3/year of brine to the sea. This treated water can be re-used instead of tap water.
Waste Avoidance and Prevention
Across all our sites we dispose waste responsibly. For example, in Israel, our waste is collected by Ecommunity, a social enterprise that hires employees with special needs to recycle outdated hardware. In this way, Ecommunity provides economic opportunity for individuals with disabilities, while addressing the challenges of waste.
Leaks
During the reported period, there were no leaks or serious environmental incidents at any of our sites.
Hazardous Waste Reduction Long-term Targets
2020 Target:
Achieved
We achieved the target set out in our previous report “to reduce sulfuric acid disposal by 20% annually, starting 2021”.
Looking ahead:
Reduce hazardous waste by 20% by 2030 compared to 2022.
Health & Safety
Good health and safety (H&S) management is an integral part of overall business strategy. With our employees at the heart of everything we do, we take health, safety and the prevention of any work-related health issues extremely seriously. All our employees are covered by our occupational health and safety management system and are expected to adhere
to outlined occupational safety policies and procedures. In order to establish a health-oriented work culture, we have ongoing health related trainings, auditing practices and safety committee oversight. Collectively, these practices, together with our employees’ dedication, ensure that H&S risks are being identified and mitigated in the work environment, including occupational safety, emergency preparedness and prevention of occupational illness.
100% of employees received health and safety training in 2023
Occupational Safety
Employee exposure to potential safety hazards (e.g., electrical and other energy sources, fire, vehicles and fall hazards) is controlled through well designed engineering and administrative controls, preventative maintenance, safe work procedures (including lockout/ tagout) and periodic safety training. Employees are provided with well-maintained, personal protective clothing and equipment as required for the specific tasks performed. Additionally, production and other machinery are being evaluated regularly for safety hazards and physical guards, with interlocks and barriers that are being used to avoid potential risk to employees.
Emergency Preparedness
We evaluate and assess the impact of potential emergency situations and events and prepare ourselves through clear emergency plans and response procedures. These include employee notification and evacuation procedures, employee training and drills, maintenance of appropriate fire detection and suppression equipment, emergency reporting and immediate and longer-term recovery plans. Our sites also have designated employee emergency response teams who are responsible to help manage the situation in case of an emergency.
Occupational Injury and Illness
Procedures and systems are in place to prevent, report, manage and track occupational injury and illness, including guidelines for employee reporting, classifying and recording injury and illness cases. When incidents do occur, we also have an investigation procedure that allows us to examine the occurrences and implement corrective actions to prevent future potential cases. Safety trainings specifically focus, among others, on exposure to chemicals or gases, required work procedures to ensure proper handling thereof and measures to be taken in the event of any such exposure, event or injury.
Management Approach
Tower is certified by ISO 45001 Occupational Health and Safety (H&S) international standard. To ensure compliance with the standard, Tower has in place an executive leadership structure that is accountable for the health and safety of all employees, helps define required work procedures, and is responsible for reporting and system oversight.
H&S Functional Structure
We have established H&S committees at all of our sites which are composed of both leadership members and operational employees. From 2021 to 2023, we had 31 members on our health and safety committees globally of which 16 were operational employees.
The committee holds meetings frequently to allow for consistent oversight. In 2022 and 2023, 31 meetings took place annually. Safety committees are informed of every accident and incident in order to investigate and prevent such future events.
At Tower, we engage every level of the H&S operation to ensure compliance with international standards and protection of all employees, site visitors and contractors. The CEO is at the top of this hierarchy of responsibility, followed by the COO and SVP of Excellence & QA, and each site has a local Safety Management team.
Monitoring and Managing Risks
Each Tower facility has a Safety Team that works in a cross-functional capacity to ensure that adequate safety protocols are in place and are properly executed. Our safety teams on each site assist with distribution of information, performing audits/inspections, monitoring and reporting H&S concerns, and implementing job hazard analysis and risk assessments.
The overall success of risk management is ensured by constant communication within our entire operation. We maintain this dialogue through daily facilities team meetings and online “ticket” systems that allow employees to submit issues of concern as they occur.
In addition to upholding the requirements according to ISO 45001 international standard, we perform a wide range of audits throughout our fabs to ensure the health and safety of our teams. These audits are both internal and external and are performed regularly to ensure continued compliance. Our internal H&S audits and risk surveys are preforming at a high-frequency throughout the year with an average of 257 audits or surveys taking place annually between 2022 and 2023. Through our internal and external audits, we have identified that the main risks at Tower are hazardous gases, chemicals, radiation and electrical risks. In order to minimize these risks, Tower has a number of protective systems, including engineering defense, administrative protection, monitoring, personal protective equipment and an ERT (emergency response team).
Employee Awareness and Engagement
In order to strengthen awareness among, and engagement of employees, all the H&S information is accessible on the internal “H&S site” as well as on the corporate bulletin board. Additionally, H&S meeting and audit report summaries, accidents and events are published on that platform for employees’ awareness. Employees are asked to submit comments and advice based on prior experience with respect to accidents, incidents or near-miss events to minimize and prevent future events.
Annual H&S Training
We provide safety training to employees and relevant contractors both in person and online. Training includes annual safety training for 100% of employees, health and safety orientation for new employees, and specialized safety training for employees based on their role type. For example, employees performing equipment maintenance will receive additional trainings on hand powered tools and working at heights, as well as other applicable topics. Other examples of our safety training areas include foundational aspects such as fall prevention, ergonomics and first aid, as well as additional specialized areas including machine safety, hazardous material, radiation safety and electrical safety. Lastly, employees also receive training on our EHS system as a whole, including on our ISO 45001 and ISO14001.
H&S Performance
We closely monitor our H&S indicators in order to ensure consistent performance. Each of Tower’s sites EHS managers reports monthly on accidents (for any event in which an employee lost more than one working day), incidents (safety event where employees didn’t lose any working days), near-miss events and injuries categorized by cause of event. During 2022 and 2023 the total number and rate of accidents has decreased and during this period of time, there were no on-site fatalities. During the report period, the Company did not suffer any monetary losses as a result of legal proceedings associated with employee health and safety violations.
2022 | 2023 | |||
Number | Rate | Number | Rate | |
The number and rate of high- consequence work-related injuries (excluding fatalities) | 8 | 0.18 | 4 | 0.12 |
The number and rate of recordable work-related injuries | 29 | 1.10 | 16 | 0.47 |
* The injury rate is calculated in alignment with the GRI standard methodology as follows; Injury Rate = (work related injuries/the number of hours worked) x 200,000 working hours
2022 | 2023 | |||
The number and rate of fatalities as a result of work-related injury or ill health | 0 | 0 | ||
The number of cases of recordable work-related ill health | 0 | 0 |
Long-term Target
We continue to work towards our long-term target set in our 2020 report; to reduce the number of accidents by at least 50% by 2030 by continuous improvement of our safety process and
procedures.
Social Responsibility: Employees & Work Environment
At Tower, we believe that our employees are the foundation of our success, and that empowering them to reach their professional and personal potential is a critical component in moving our enterprise forward.
To advance this vision, we strive to sustain a culture of learning and development that encourages our employees to exert their best efforts while growing within the company.
As a company, our approach to workplace and employee development is grounded in the principles of inclusivity and fairness, fostering innovation and creativity to make an impact, and add value in our global corporate activities.
We have more than 3,000 employees as of the end of 2023, representing a global community with sites spread worldwide. Our team of professionals are highly devoted, talented, and creative with broad
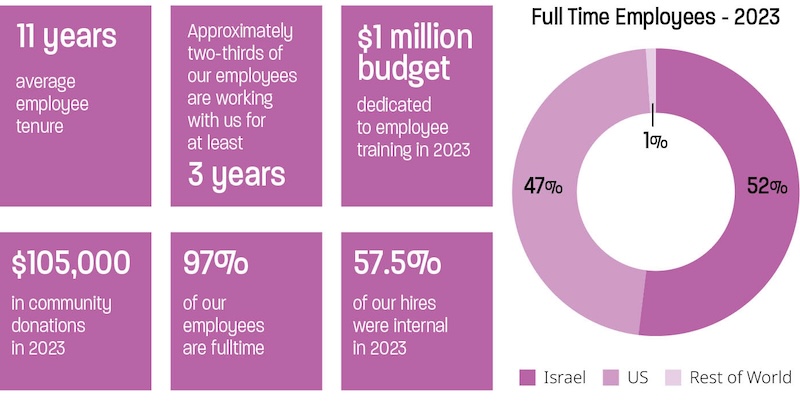
Where We Are Today | Our Goals | |
Gender Diversity | We provided women unique growth opportunities through our women’s forum and mentoring partnerships. This year, women made up 30% of our total workforce and 22% of our top management positions. | Continue creating an environment that supports gender equality in the work-place through the introduction of new and on-going programs (see ‘Gender Diversity’ for program list). |
Learning and Development | We have an internal mobility rate of 3.7% and an average employee tenure of 11 years. Our successful employee retention is achieved through a consistent focus on creating an enriching career full of learning and growth opportunities. | To achieve our overarching goal for consistent professional development for our employees, we plan to achieve an internal mobility rate between 7% to 10% of employees. |
Top Talent Employee Retention | 2.4% turnover rate for top talent in 2023. | To reduce top talent turnover to less than 2% annually. |
Developing and Engaging Our Employees
At Tower, we consider investment in employee experience and development to be vital in fostering a positive environment that enables employees to realize their full potential and advance our business. To support this commitment, we allocated a budget of 1,167,000 USD to employee training in 2023 alone.
Driving Employee Engagement
People spend a significant portion of their day at work, and it is our aim that they feel that their time and effort is contributing to a meaningful purpose. At Tower, we make every effort to enhance our employees’ well-being and ensure that they feel connected to the company’s vision, to one another, and to the values we collectively uphold.
Connecting New Hires to Tower’s Mission and Values
New hires participate in a dedicated training program that equips them with professional skills and imparts knowledge about the company’s culture, customers, values, technology and more. The in-person on-site orientation is guided by professionally trained on-boarding team members and is thoughtfully designed to offer new hires a warm and innovative welcome. Alongside ensuring that they have all the necessary information for their health and safety, we also provide insight into the opportunities and pathways available for them to advance, grow and lead successful careers within the company.
Fostering a Culture of Connection
To foster an open and approachable environment and strengthen the bond between company leaders and the workforce, we conduct global meetings between senior leaders and employees. These meetings serve as a platform for open and candid conversations, enabling attendees to directly pose questions to the leaders and discuss matters that are important to them.
Connecting Across the Globe
As part of our continuous commitment to strengthening connections among employees across different sites, we organized various global engagement activities throughout the year. One noteworthy example in 2023 was our global escape room event. The escape room was a resounding success, with groups developing camaraderie as they collaborated to solve riddles in a friendly and competitive atmosphere.
Promoting Knowledge Sharing
Ensuring and promoting a high level of knowledge sharing within a company is pivotal for fostering innovation, enhancing collaboration and maximizing the collective intelligence of the organization, especially in the presence of language and geographical barriers. That is why Tower conducts company-wide campaigns focused on knowledge sharing on a routine basis aimed at encouraging information exchange across sites and efficient problem-solving. Knowledge sharing occurs in numerous ways and through different channels such as Gate – Tower’s “google- like” professional search engine and professional communities’ monthly meetings.
Staying in Touch
To keep employees connected and engaged, we publish a weekly newsletter that includes details about our teams’ participation in conferences, press releases, training and development initiatives, welfare offerings, volunteering opportunities and more.
Instilling a Sense of Purpose and Resilience at Work
Employees in all companies, particularly in the tech industry, are contend with volatility, uncertainty, complexity and ambiguity (VUCA). We are committed to enhancing our employees’ resilience so they can confidently confront and adapt to changes and challenges, allowing them to thrive in the work environment. Research indicates that robust, positive connections contribute to resilience. As such, Tower proactively organizes learning sessions, meetings with management, interactions with customers and gatherings with people from all sites to foster a stronger sense of connection among employees, teams and global sites.
We engage experts to share tools from positive psychology and practices for happiness and resilience at work. We ensure that this content is accessible and tailored to various populations. These activities promote teamwork, foster collaboration, enhance problem-solving skills and encourage effective communication under pressure.
Creating a purpose-driven work environment also entails connecting with the community around us. You can learn more about our community service initiatives in ‘Bringing Value to Our communities’.
Growth and Development
Research underscores the significance of learning in order to maintain brain health and a high quality of life as individuals age. We firmly believe that organizations play a central role in adult development and gladly embrace this responsibility. Our development programs are aligned with Tower’s Annual Strategic Plan (ASP) and the Annual Operating Plan (AOP). These versatile programs encompass a wide range of subjects, including tailored technical courses for different employee populations and across different levels of professional development from entry to leadership.
Growth and Development Long-term Target and Strategy:
Our Target: achieve an internal mobility rate between 7% to 10%.
Potential Action Steps to Reach our Target:
- Initiate additional dedicated career development programs which provide comprehensive development options through training, upskilling and cross-functional training opportunities.
- Enhance our internal mobility framework that facilitates the movement of employees across different roles, departments and locations within the company.
- Grow our existing mentorship and coaching options to help employees navigate their career paths, providing guidance and support for their professional growth and mobility.
- Reinforce our individual development plans (IDP) that help employees align their career aspirations and the organization’s strategic goals, ensuring a clear pathway for growth.
- Further provide global mobility opportunities for relevant employees to work in different geographic locations, gaining international experience and broadening their perspectives.
- Define clear company reward systems that acknowledge and incentivize employees’ efforts towards career development and mobility within the organization.
General Learning Platforms |
Orientation Training LinkedIn Learning Workshops, Lectures and Knowledge Sharing |
Manager Development |
Section Managers’ Pipeline Production Section Manager Development Management Academy |
Leadership Growth |
LEAD Program BUILD Program for Directors
|
Offering Personalized and Accessible Online Learning Solutions
We are dedicated to delivering the optimal learning experience for our employees through a range of methods, including practical workshops, online courses, high-quality content development services (such as Articulate platform), and instructor-led classroom sessions. Our LinkedIn Learning platform offers over 16,000 online courses and is directly integrated into our wider Learning Management System (LMS). Currently, more than 70% of our relevant employees are using this resource.
Tower Technical Journal
Personal development and advancement at Tower are also linked to the publication of articles in the TTJ (Tower Technical Journal). The TTJ is an internal, peer-reviewed journal dedicated to fostering the sharing of information and experiences in the field of semiconductor technologies among our engineers. It features technological and marketing reviews, research papers, research notes, tutorials and case studies that reflect the latest developments and advancements in our facilities and in our engineering departments as a whole.
Professional Leveling program
Our Professional Leveling Platform serves as a professional roadmap, facilitating and incentivizing the enhancement of qualifications and expertise for employees across various departments. This program caters to our engineering, technicians, operators, and corporate professional cohorts. The platform is meticulously designed to effectively gauge an individual’s proficiency and performance within the organization and help guide them through each level of their skills development. Through this initiative, we are dedicated to nurturing a culture of continuous improvement and excellence, ultimately enabling our employees to realize their full potential, reach a high sense of achievement and contribute to the success of our business.
Operators Development programs
At Tower, recognizing the pivotal role of our operators, we have established dedicated development programs tailored to their unique skill sets and career aspirations. The first stage emphasizes their development within their current roles and fosters a comprehensive understanding of their responsibilities. The second stage offers opportunities for advancement within the production department or other relevant departments within Tower. Moreover, our commitment to their professional development extends beyond the organization, as we offer an annual scholarship program enabling operators to pursue academic studies in areas that align with their interests and have the potential to drive their growth within Tower. By providing a multifaceted approach to development, we promote the empowerment of our operators and provide a path for their sustained success in our dynamic work environment.
Supporting Academic Pursuit Through Employee Scholarships
Tower provides professional development and long-term academic study opportunities to eligible employees. Key to this offering is our partnership with the Industrial Engineering Department at Tel Aviv University and Arizona State University. Presently, we are proud to be supporting seven employees in pursuit of their Master of Science (MS) program in Industrial Engineering.
Furthermore, the Company offers a scholarship program aimed at supporting employees’ academic studies in fields that can contribute to their professional growth within Tower. This program covers the tuition fees for more than 50 employees worldwide each year.
Building A Professional Leadership Pipeline
At Tower, we strongly believe in nurturing leadership from within the organization and maintaining a robust and growing leadership pipeline. We recognize that building a strong leadership cadre is not only crucial for our business success but also for fostering an inclusive corporate culture and enhancing individual growth. To achieve this, we design and implement programs that facilitate the smooth transition of our leaders to their next managerial level.
Production Section Manager Development
At our Israel site, we conduct quarterly forum meetings with 50 production managers in which we address various managerial and leadership topics such as learning from mistakes, operator retention, and discipline in the production line. Additionally, we incorporate procedure refreshers and soft skills training as part of our annual plan.
These meetings play a crucial role in promoting inclusive and people-centric leadership within our operations. This initiative is gradually expanding beyond our Israel site and will soon be implemented at our San Antonio site.
Section Manager’s Pipeline
As part of our commitment to providing every production line employee with opportunities to build a career at Tower, we run an annual program in Israel designed to identify and nurture the next- generation of section managers. Tower’s pipeline program is open to all operators. The program includes a professional selection process involving assessment centers, individual interviews, and an admissions committee. Our section management is broken down as follows:
- Top Management – CEO and three levels below, defined as SVP, VP, and Directors.
- Junior Management – first level management, defined as Section Heads, Production SVs (section managers) and Managing GLs.
Tower Management Academy
Tower Management Academy is our micro- skills workshops framework that is open to all leaders within the organization. The academy provides hands-on, practical, and focused skill- building practices, covering topics like impactful communication and strategic decision-making, to foster high-performance teams and teach how to lead with a sense of ownership.
Lead Program
Each year, approximately 50 of our employees’ transition into managerial roles. To ensure that they are set up for success, our ‘New Managers Program’ provides four key components:
- Monthly, face-to-face sessions that equip them with tools on how to lead effectively.
- A 360-degree feedback report after one year in the managerial role.
- Coaching meetings with the HR team to support their growth.
- Access to on-demand content through our learning system.
Build Program for Directors
When an individual is promoted to the role of Director at Tower, they are presented with the opportunity to cultivate advanced leadership capabilities through a specialized program known as BUILD for Directors. This program involves gathering upward feedback, followed by one-on-one support from the HR department, and learning modules that offer skills and knowledge for ongoing enhancement. In 2023, 55 Directors from all our sites participated in this program.
Developing and Retaining Top Talent
At any given time, there are approximately 200 employees whom we have identified as “key talents” within our organization. These individuals represent our rising stars, possessing the highest potential for growth, unique or substantial impact and exceptional capabilities. Our investment in their development is crucial to maximizing their future with the company. We have also established specific programs to support our key talents in unlocking their potential which include:
- Career Management – a total of 75 key talents participated in the “Be Bold in Your Career” program. This program spanned 10 weeks and included live webinars, peer coaching and practical assignments, all supported by career development experts.
- Individual Coaching – we provided individual coaching to 48 key talents who identified specific challenges, problems or events they wanted guidance on.
- Individual Development Plans (IDP) – we conducted hands-on IDP workshops in both Israel and the United States and distributed an ‘IDP Guide’ and ‘IDP Template’ to help employees define the goals they wish to attain and formulate their own development plans
Approximately two-thirds of our employees are working with us for at least 3 years, with 11 years as the average employee tenure.
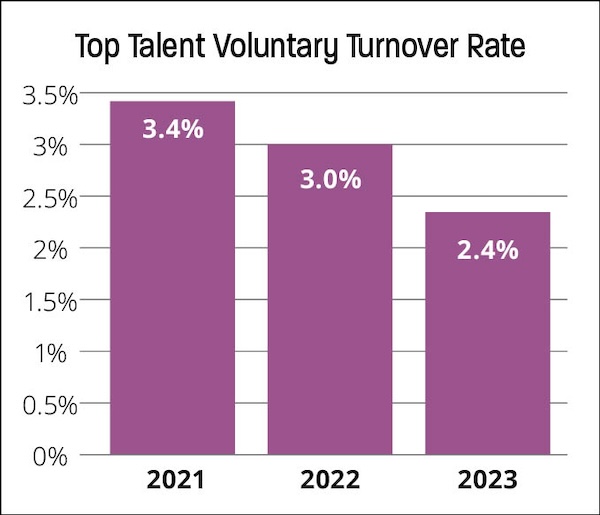
Top-Talent Retention Long-term Target:
Reduce turnover of our top 20% talent to ≤2% annually.
Employee Performance Review
Tower’s commitment to a fair and transparent method of assessing employee performance is essential to the success of our company. As part of our company policy, all employees undergo an annual evaluation process.
The process framework encompasses employees’ business and performance goals, as well as development goals and evaluations based on the company’s values. The employee assessment procedure includes a self-evaluation and the manager’s assessment. These evaluations lead to a leveling adjustment, and, when applicable, merit- based salary adjustments.
Employee Well-Being and Recognition
At Tower, we hold the well-being of our employees and their families in high regard. Our employees are eligible for a range of benefits linked to their performance and length of service. We also recognize employees’ tenure with seniority gifts, granted every ten years, and celebrate birthdays and holidays with presents. Every year, we hold certain celebrations with spouses, offer family outings, invite employees’ families to events and holiday celebrations, and organize kids’ activities for employees’ families.
100% of employees take part in annual performance review
These activities strengthen our community and connect employees’ families. This holistic approach enhances the sense of belonging that extends beyond the workplace, improving overall satisfaction and engagement.
Celebrating Employee Achievements
Tower’s nurturing and empowering environment inspires employees to be efficient, innovative, and motivated. On a quarterly basis, we celebrate and reward the achievements of teams and individuals who have excelled in their contribution.
Our CEO acknowledges and rewards high-performing employees with prizes in an annual award ceremony.
Succession Planning and Internal Mobility
At Tower, we place special emphasis on internal talent recruitment. Annually, Tower implements a comprehensive procedure to identify potential successors for critical employees and managers. This process ensures that contingency plans are in place to promote the most suitable candidates from within the company should a critical employee or manager decide to leave their position.
We are committed to investing in the company’s future and creating opportunities for our employees.
In 2023, our internal hiring rate stood at approximately 57%, as well as an impressive turnover rate of approximately 10%.
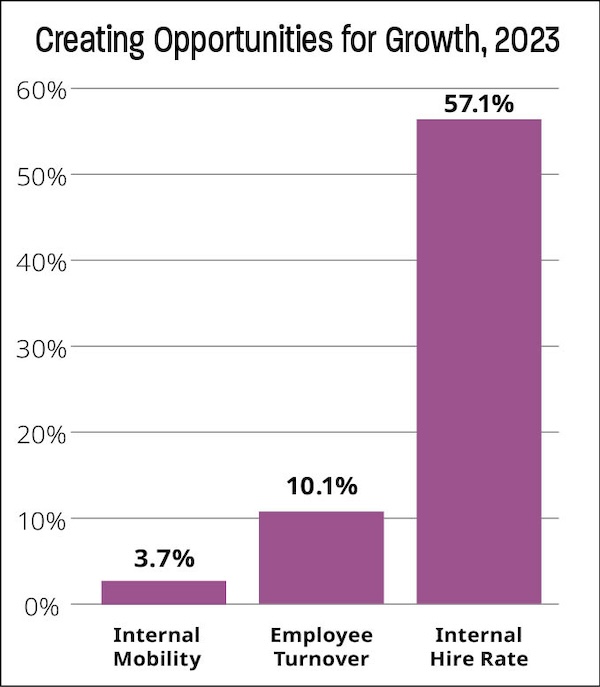
Diversity and Inclusion
Tower is a diverse company with employees from various countries, cultures, religions and genders. Women and men spanning from 18 to 78 years old all working together side by side. We believe that a diverse work environment brings people together, encourages creativity and enables the Company to use individual and cultural strengths to improve and achieve our common goals. Our corporate culture emphasizes respect, recognition and opportunity for all employees to thrive and grow. We work closely with various non-profit organizations focused on promoting diverse hiring across different sectors including above the age of 50, immigrants and other underrepresented populations.
Promoting Gender Equality in the Workplace
In 2023, 30% of our global workforce was represented by women, and 22% of our top management was composed of female leaders.
Tower is committed to gender equality and promoting a fair and inclusive environment. We believe in equal opportunity, and focus on the ability, talent and capabilities of our employees. The Company supports internal promotions, enabling operators to start their career and grow to higher positions within the company.
In order to achieve equitable pay practices, we monitor our gender wage gap across our operations. In Israel, we publish our gender wage gap report according to local regulation, while in the US, we submit an annual ‘Equal Opportunity Report’ to the Department of Labor. In Israel, the results showed that female employees in most positions are paid similarly to male employees in the same role, and, in some role types, even earn on average more than their male counterparts. Where gaps may exist, we strive to improve and reduce any potential threshold of inequality.
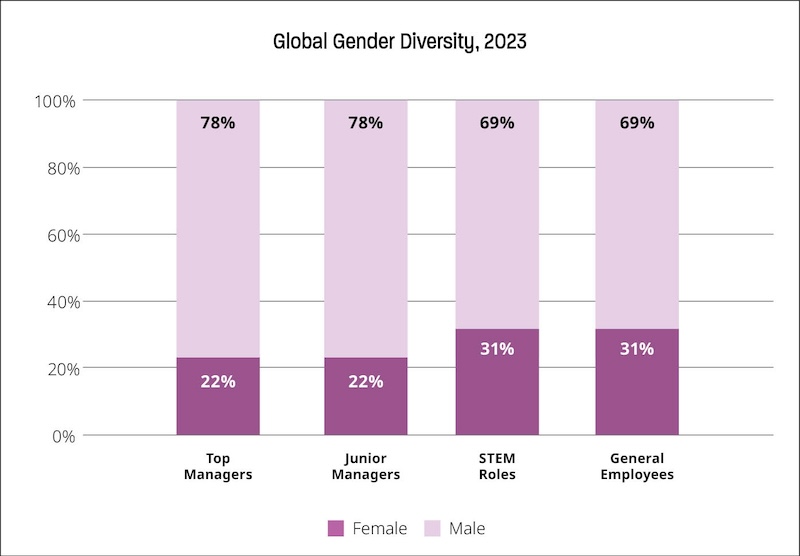
Women’s Career Mentoring Initiative
In 2022, Tower launched a global one-on-one mentoring program for female employees, with the aim of supporting their professional growth, offering guidance, and advancing gender diversity and inclusion within the organization. A total of 22 mentor- mentee pairs participated in this program, and we plan to introduce additional cohorts in the future.
Furthermore, female employees were invited to attend lectures and workshops aimed at equipping them with valuable personal development skills, and most importantly, boosting their self-assurance in recognizing their own value.
Women’s Career Forum
We organized two women’s panel discussions on the topic of women’s career choices, featuring senior leaders as panelists, with one held in Israel and the other in the US. Both sessions sparked lively and stoked heartfelt discussions that reflected the controversial nature of the topic.
Gender Equity Long-term Target and Strategy:
Strengthen gender equality.
Potential Action Steps to Reach our Target:
- Grow our mentorship programs which pair female employees with experienced mentors to guide their career development and provide them with insights on navigating the corporate landscape.
- Provide leadership development workshops tailored to developing leadership skills, with a focus on empowering women to take on managerial roles.
- Continue providing flexible work policies that support work-life balance, and make it easier for women to pursue career advancement opportunities while managing personal responsibilities.
- Establish inclusivity from the starting-line through inclusive recruitment practices which are designed to attract and hire a diverse pool of candidates, with a focus on increasing the representation of women in managerial and leadership positions.
- Continue to regularly monitor and report our progress on gender equality initiatives, to track advancements and identify areas for improvement.
- Provide unconscious-bias training to the recruitment teams.
Achieving our prior goals: We have achieved the gender equality targets set in our previous report through our establishment of the women’s forum and mentorship program.
Equal Opportunity Employer
At Tower, we are committed to create an inclusive work environment and strive to continually increase minority groups’ representation in all of our sites.
Mr. Russell Ellwanger, Tower Semiconductor CEO: “The ideal of a civil society with equal opportunities and rights is not easy to achieve, but it is also not an illusion. It begins with corporate leaders who live and enforce an ethical, moral and inclusive value system with no exceptions.”
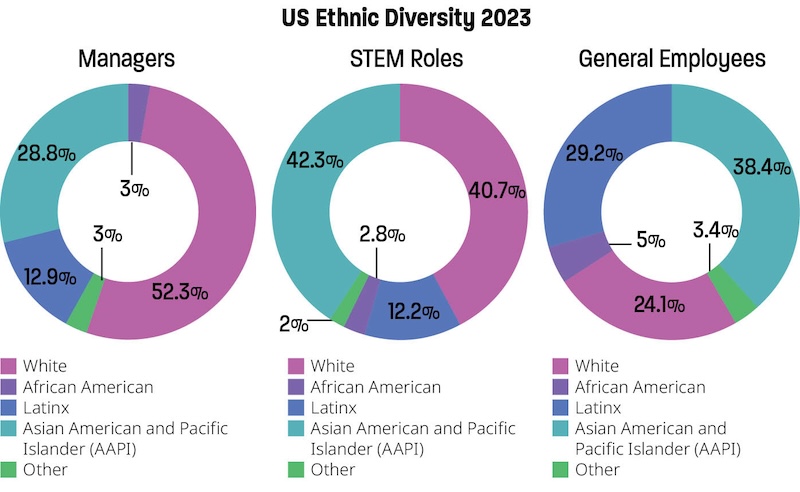
Empowering Employees with Disabilities
In our hiring processes, we give equal opportunity to populations with disabilities.
In addition, we participate in specialized job fairs sponsored by local non-profit organizations that focus on employment of people with disabilities in order to outreach and provide meaningful job opportunities. We also encourage our existing employees to voluntarily report any personal disabilities so that we may offer adjustments as may be needed in the workspace. The Employing Persons with Disabilities Policy is available on our website.
Labor Rights in the Workplace
As an organization, we consider a zero-tolerance policy towards harassment and discrimination, as part of our core values. We are committed to the health, safety and labor rights of our employees and provide our managers with the necessary tools in order to lead the Company in accordance with this policy.
For more information, please refer to ‘Labor and Human Rights’ in the ‘Responsible and Ethical Business’ chapter of this report.
Bringing Value to Our Communities
Corporate social responsibility is an integral building block of our success, essential for fostering a healthy and balanced corporate culture, and contributing to global betterment. We support a wide range of community-building activities, with a special focus on promoting Science, Technology, Engineering, and Mathematics (STEM) education and supporting nature. We contribute to the communities where we operate through job creation, economic opportunities and financial and volunteering donations.
Our employees volunteering hours have also increased steadily from 2021 to 2023, with a growing number of employees engaged in our various community initiatives.
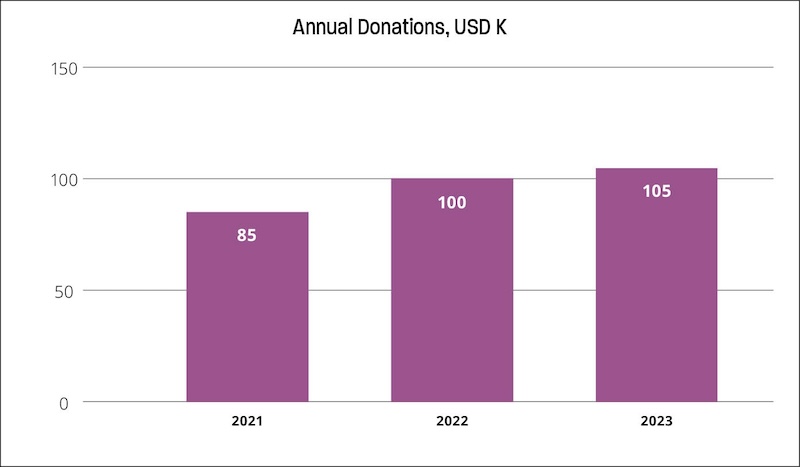
Standing Strong In Times Of Crisis
During the recent period of conflict in Israel, Tower, defined by the local authorities as an essential facility, stayed true to its core principles of social responsibility. Recognizing the impact on its employees and the community, Tower implemented various initiatives to demonstrate solidarity and support.
Supporting Our Heroes:
Reserve Soldiers and Their Families
- Essential Care Packages: over 100 Tower employees were called to reserve duty. To express gratitude and ensure their well-being, Tower provided essential equipment packages containing mattresses, thermal clothing, food provisions, power banks and technical gear.
- Sabbath Packages for Families: understanding the challenges faced by the families of reservists, Tower sent special Sabbath packages filled with thoughtful items, offering a small gesture of care and solidarity during this difficult time.
Empowering Local Agriculture in Conflict Zones
- Supporting Farmers: recognizing the struggles of farmers in conflict-affected areas, Tower proactively purchased agricultural products from them to alleviate their financial burdens and support local agriculture during these challenging times. The produce was then packaged and distributed to our employees.
- Volunteer Power: Tower employees went beyond financial contributions by volunteering their time and labor to assist farmers in need. This exemplified the company’s dedication to community support through hands-on action.
Ensuring Smooth Reintegration for Returning Employees
- Managerial Guidance: Tower provided managers with guidance on offering support to employees returning from military service, ensuring a smooth transition back to work.
- Welcome Back Packages: each returning employee received a thoughtful package, symbolizing the organization’s unwavering support and appreciation for their service.
Investing in Employees Well-being
- Stress Management Training: recognizing the potential impact of stressful times, Tower offered training sessions on coping mechanisms and meditation to help improve the overall well-being of its employees.
These initiatives showcase Tower’s unwavering commitment to corporate social responsibility. By actively contributing during a crisis, Tower demonstrates its deep sense of solidarity and support for its employees, their families and the broader community. Tower’s actions go beyond the realm of its operations, making a positive and impactful contribution to society.
Supporting Student Research and Environmental Engagement
Supporting Global Awareness Investigation and Action (GAIA) Program
The GAIA Project is an environmental research project designed to increase student awareness of local environmental concerns and encourage active community-based efforts towards their resolution. The GAIA Project, led by Dr. Stuart Fleisher, is a part of the Walworth Barbour American International School in Israel (WBAIS). For over a decade, Tower has been a platinum sponsor and has also provided mentorship to the GAIA program, which works to instill “Peaceful Cooperation in a Green World” through activities for middle and high school students. We are excited to continually provide tools and counsel to young student-citizen-scientists, guiding and empowering them to take proactive and immediate action addressing the environmental challenges of our time
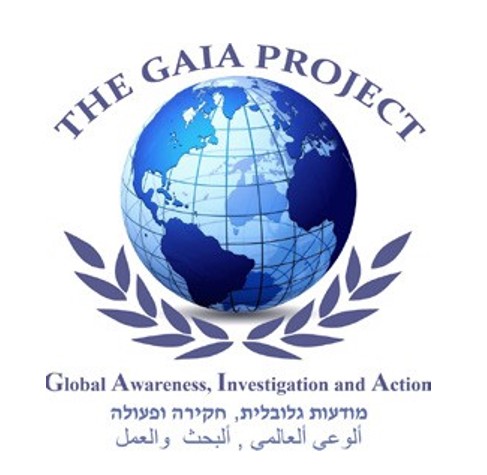
Middle and high school students from various schools and socio-economic backgrounds across Israel, as well as from the Czech Republic, Greece and Uganda, are enrolled in GAIA. They work collaboratively under the guidance of mentors to identify specific questions about topics of interest or concern in their local communities. Through scientific research, community engagement and sharing collected data with their local and international network, they work towards developing and implementing a sustainable solution. A typical research question will need 3-5 years of data collection and analysis before the team issues a final summary and their recommended solution.
Tower supports a number of GAIA projects, including wildlife preservation, endangered species sanctuaries (with guidance from the Wildlife Alliance in Cambodia), recycling of materials (up-cycling) to produce quality goods, biological pest control, water conservation, hydroponic indoor gardens, reductions in marine pollutions, among others.
Encouraging STEM education
Tower encourages our engineers to share their backgrounds and passion for science with students, promoting opportunities for future careers in science and technology. In 2023, we hosted school-age and university students at our facilities in Israel and California to increase their awareness and knowledge of the semiconductor industry. These visits provided insights into our advanced technology and production processes, allowing students to experience the hands-on, day-to-day work of our engineers and learn about the different career paths one can pursue within the semiconductor industry.
TechnoWizards
In San Antonio, TX, Tower is the largest sponsor of the TechnoWizards, a grade school group of students that compete in ideation, execution and presentation of original robotics creations. The students compete at the state and national level and share their creations with Tower employees and their families.
Language and Math Skills
Our employees take part in an English learning project which gives youth in Israel an opportunity to learn English and improve their communication skills, in the hopes of helping them gain access to more opportunities in the future. In addition, as part of a new initiative, we began teaching math at a local high school in Migdal HaEmek, Israel..
Big Brother Program
For almost two decades, employees at our HQ (Migdal Haemek) facilities are supporting youth clubs for kids who need help with their homework or need some emotional support. A team of about 15 volunteers participate in this activity once a week.
Educational Supplies & Holiday Presents
In Texas, Tower purchased a significant quantity of school supplies, and our employees filled 250 backpacks with school supplies to support children in need within the community. Additionally, during the holiday season, Tower bought 400 educational toys as a holiday gift for underprivileged children, and our employees volunteered to wrap these gifts in time for the holidays.
Food Bank Events
We help provide food for families in need in the communities where we operate by participating in local food bank events. In 2023, our employees in California, Texas, and Israel volunteered to sort, pack and distribute food packages in their local communities. At the company’s San Antonio, TX facility, our employees contributed to the community by supporting a local food bank event. They packed over 19,000 lbs. of food, translating to over 15,000 meals for families in need in the area.
SUPPORTING NATURE
For Earth Day, we provide our employees with the opportunity to serve the community. Last year, employees from our Newport Beach, CA site helped weed out over 25 large bags worth of invasive plants in the Newport Beach Back Bay. These invasive plants have the potential to displace native plant communities and wildlife, therefore, removing them helps protect the environment and ensure the area will thrive in years to come!
Good Deeds Day is an international celebration of DOING GOOD! This year every department in Migdal Haemek chose where it wanted to do a good deed. Most departments chose to help with projects related to agriculture or archaeology.
GRI Disclosure Number | GRI Disclosure Title | Section Title |
2-1 | Organizational details | Introduction Ch. – About the Company and Our Global Operations |
2-2 | Entities included in the organization’s sustainability reporting | About this Report |
2-3 | Reporting period, frequency and contact point | About this Report |
2-4 | Restatements of information | No restatements have been made from prior report. |
2-5 | External assurance | N/A |
2-6 | Activities, value chain and other business relationships | Introduction Ch. and Facilitating a Sustainable Future Ch. |
2-7 | Employees | Employees & Work Environment Ch. – Introduction, Diversity and Inclusion |
2-8 | Workers who are not employees | N/A |
2-9 | Governance structure and composition | Responsible and Ethical Business Ch. – Our Board of Directors |
2-10 | Nomination and selection of the highest governance body | Responsible and Ethical Business Ch. – Our Board of Directors |
2-11 | Chair of the highest governance body | Responsible and Ethical Business Ch. – Our Board of Directors |
2-12 | Role of the highest governance body in overseeing the management of impacts | Responsible and Ethical Business Ch. – Our Board of Directors; ESG Governance, CGN Committee |
2-13 | Delegation of responsibility for managing impacts | Responsible and Ethical Business Ch. – Our Board of Directors |
2-14 | Role of the highest governance body in sustainability reporting | The report is approved by the board of directors. |
2-15 | Conflicts of interest | Global Code of Ethics |
2-16 | Communication of critical concerns | Global Code of Ethics |
2-17 | Collective knowledge of the highest governance body | Responsible and Ethical Business Ch. – Board Skills Matrix |
2-18 | Evaluation of the performance of the highest governance body | Responsible and Ethical Business Ch. – Our Board of Directors; Our 2023 20F |
2-19 | Remuneration policies | Our 2023 20F Responsible and Ethical Business Ch. – Our Board of Directors; Compensation Committee |
2-20 | Process to determine remuneration | Our 2023 20F Responsible and Ethical Business Ch. – Our Board of Directors; Compensation Committee |
2-21 | Annual total compensation ratio | N/A |
2-22 | Statement on sustainable development strategy | Environmental Responsibility Ch. – Our Long-term Environmental Impact Strategy |
2-23 | Policy commitments | Global Code of Ethics; Responsible and Ethical Business Ch. – Ethical Business Practice, Labor and Human Rights |
2-24 | Embedding policy commitments | Global Code of Ethics; Responsible and Ethical Business Ch. |
2-25 | Processes to remediate negative impacts | Responsible and Ethical Business Ch. |
2-26 | Mechanisms for seeking advice and raising concerns | Responsible and Ethical Business Ch. – Ethical Business Practice; Whistleblower Policy |
2-27 | Compliance with laws and regulations | Responsible and Ethical Business Ch. |
2-28 | Membership associations | N/A |
2-29 | Approach to stakeholder engagement | Introduction Ch. – Our Stakeholder Engagement Overview |
2-30 | Collective bargaining agreements | Responsible and Ethical Business Ch. – Ethical Business Practices |
3-1 | Explanation of the material topic and its Boundary | About this Report |
List of material topics | About this Report | |
3-3 | Management of material topics | See targets listed per topic in each chapter |
201-1 | Direct economic value generated and distributed | Our 2023 20F |
201-2 | Financial implications and other risks and opportunities due to climate change | Environmental Responsibility Ch. – Environmental and Climate Risk Management |
205-2 | Communication and training about anti- corruption policies and procedures | Responsible and Ethical Business Ch. – Our Board of Directors |
205-3 | Confirmed incidents of corruption and actions taken | Responsible and Ethical Business Ch. – Our Board of Directors |
206-1 | Legal actions for anti-competitive behavior, anti-trust, and monopoly practices | Responsible and Ethical Business Ch. – Our Board of Directors |
302-1 | Energy consumption within the organization | Environmental Responsibility Ch. – Energy Performance |
302-4 | Reduction of energy consumption | Environmental Responsibility |
303-2 | Management of water discharge-related impacts | Water Recycling, Hazardous Waste |
303-3 | Water withdrawal | Environmental Responsibility Ch. – Water management |
303-4 | Water discharge | Environmental Responsibility Ch. – Water management |
303-5 | Water consumption | Environmental Responsibility Ch. – Water management |
305-1 | Direct (Scope 1) GHG emissions | Environmental Responsibility Ch. – GHG Footprint and Energy Management |
305-2 | Energy indirect (Scope 2) GHG emissions | Environmental Responsibility Ch. – GHG Footprint and Energy Management |
305-4 | GHG emissions intensity | Environmental Responsibility Ch. – GHG Footprint and Energy Management |
305-5 | Reduction of GHG emissions | Environmental Responsibility Ch. – GHG Footprint and Energy Management |
306-1 | Waste generation and significant waste- related impacts | Environmental Responsibility Ch. – Waste Management |
306-2 | Management of significant waste-related impacts | Environmental Responsibility Ch. – Waste Management |
306-3 | Waste generated | Environmental Responsibility Ch. – Waste Management |
306-4 | Waste diverted from disposal | Environmental Responsibility Ch. – Waste Management |
306-5 | Waste directed to disposal | Environmental Responsibility Ch. – Waste Management |
401-1 | New employee hires and employee turnover | Employees & Work Environment Ch. – Developing and Engaging Our Employees |
401-2 | Benefits provided to full-time employees that are not provided to temporary or part- time employees | Employees & Work Environment Ch. – Developing and Engaging Our Employees |
403-1 | Occupational health and safety management system | Health and Safety Ch. |
403-2 | Hazard identification, risk assessment, and incident investigation | Health and Safety Ch. |
403-4 | Worker participation, consultation, and communication on occupational health and safety | Health and Safety Ch. |
403-5 | Worker training on occupational health and safety | Health and Safety Ch. |
403-6 | Promotion of worker health | Health and Safety Ch. |
403-7 | Prevention and mitigation of occupational health and safety impacts directly linked by business relationships | Health and Safety Ch. |
403-8 | Workers covered by an occupational health and safety management system | Health and Safety Ch. |
403-9 | Work-related injuries | Health and Safety Ch. |
403-10 | Work-related ill health | Health and Safety Ch. |
404-1 | Average hours of training per year per employee | Health and Safety Ch. |
404-2 | Programs for upgrading employee skills and transition assistance programs | Employees & Work Environment Ch. – Developing and Engaging Our Employees |
404-3 | Percentage of employees receiving regular performance and career development reviews | Employees & Work Environment Ch. – Developing and Engaging Our Employees |
405-1 | Diversity of governance bodies and employees | Employees & Work Environment Ch. – Diversity and Inclusion |
405-2 | Ratio of basic salary and remuneration of women to men | Employees & Work Environment Ch. – Diversity and Inclusion |
406-1 | Incidents of discrimination and corrective actions taken | Responsible and Ethical Business Ch. – Ethical Business Practice |
413-1 | Operations with local community engagement, impact assessments, and development programs | Employees & Work Environment Ch. – Developing and Engaging Our Employees |
415-1 | Political contributions | Responsible and Ethical Business Ch. – Prohibition of Political Contributions |
SASB Topic | Accounting Metric | Category | Unit of Measure | Code | Disclosure |
Greenhouse Gas Emissions | (1) Gross global Scope 1 emissions and (2) amount of total emissions from perfluorinated compounds | Quantitative | Metric tons (t) CO₂-e | TC-SC- 110a.1 | 1) Environmental Responsibility Ch. — GHG Footprint and Energy Management 2) PFC emissions are integrated into the cumulative emission totals. |
Discussion of long-term and short-term strategy or plan to manage Scope 1 emissions, emissions reduction targets, and an analysis of performance against those targets | Discussion and Analysis | n/a | TC-SC- 110a.2 | Environmental Responsibility Ch. — Our Long-term Environmental Impact Strategy | |
Energy Management in Manufacturing | (1) Total energy consumed, (2) percentage grid electricity, (3) percentage renewable | Quantitative | gajoules (GJ), Percentage (%) | TC-SC- 130a.1 | Environmental Responsibility Ch. — Energy Performance |
Water Management | (1) Total water withdrawn, (2) total water consumed, percentage of each in regions with High or Extremely High Baseline Water Stress | Quantitative | Thousand cubic meters (m³), Percentage (%) | TC-SC- 140a.1 | Environmental Responsibility Ch. — Water management |
Waste Management | Amount of hazardous waste from manufacturing, percentage recycled | Quantitative | Metric tons (t), Percentage (%) | TC-SC- 150a.1 | Environmental Responsibility Ch. – Waste Management |
Employee Health & Safety | Description of efforts to assess, monitor, and reduce exposure of employees to human health hazards | Discussion and Analysis | n/a | TC-SC- 320a.1 | Health and Safety Ch. |
Total amount of monetary losses as a result of legal proceedings associated with employee health and safety violations | Quantitative | Reporting currency | TC-SC- 320a.2 | Health and Safety Ch. | |
Recruiting & Managing a Global & Skilled Workforce | Percentage of employees that are (1) foreign nationals and (2) located offshore | Quantitative | Percentage (%) | TC-SC- 330a.1 | Employees & Work Environment Ch. — Intro |
Product Lifecycle Management | Percentage of products by revenue that contain IEC 62474 declarable substances | Quantitative | Percentage (%) | TC-SC- 410a.1 | Not available |
Processor energy efficiency at a system-level for: (1) servers, (2) desktops, and (3) laptops | Quantitative | Various, by product category | TC-SC- 410a.2 | Not applicable | |
Materials Sourcing | Description of the management of risks associated with the use of critical materials | Discussion and Analysis | n/a | TC-SC- 440a.1 | Environmental Responsibility Ch. |
Intellectual Property Protection & Competitive Behavior | Total amount of monetary losses as a result of legal proceedings associated with anti-competitive behavior regulations | Quantitative | Presentation Currency | TC-SC- 520a.1 | Responsible and Ethical Business Ch. – Ethical Business Practice |
2023 Corporate Sustainability (ESG) Report
www.towersemi.com
For more information please contact
Noit Levy | Senior Vice President of Investor Relations, Communications, and Corporate Sustainability
+972-74-7377556 | [email protected]